Sidestepping the sludge – preventing the formation of paraffin wax in low sulphur fuels
Ultra low sulphur fuels may be the key to compliant operations in Emission Control Areas (ECAs), but they can also open the door to an unwanted, and slimy guest in your vessels's engines and fuel tanks. Jonas Ostlund and Sachin Gupta of Wilhelmsen Ships Service (WSS) discuss the cold flow characteristics of distillate fuels and the formation of paraffin wax in cold temperatures.
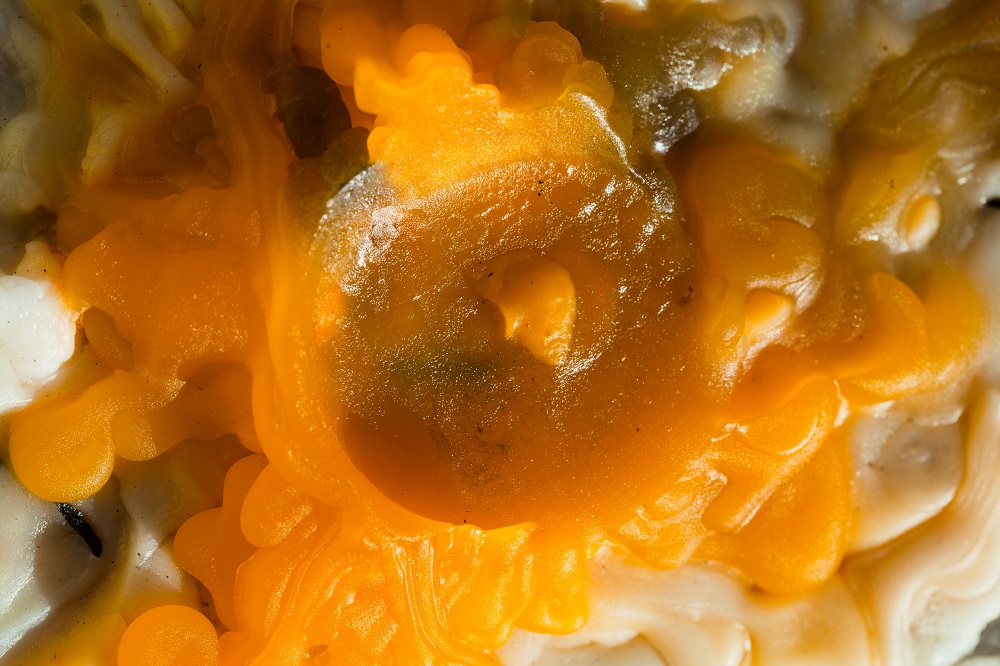
"It's like mucus,” says Jonas Ostlund, WSS Product Marketing Manager Oil .
"When a cold comes on it starts forming in your tubes. As the cold gets worse it gets thicker, slowing you down and eventually, if it gets bad enough, stopping you altogether.
"But thankfully, unlike a common cold, this can be avoided.”
Ostlund's analogy may be unpleasant, but it seems entirely appropriate for an issue that afflicts an increasing number of vessels at this time of year – the formation of wax in distillate fuels.
The problem with wax
Under the new global sulphur cap, the sulphur content of fuel oil used on board all ships must meet the 0.5% sulphur limit, while the ECAs will remain at the 2015 standard of 0.1% content.
The installation of a scrubber provided one path to compliance, while switching to alternative fuels and distillates opened up another. The distillate option has proved popular for its relative simplicity and cost effectiveness, but it does come with challenges, particularly during wintertime.
"As temperatures drop the wax problem increases,” explains Sachin Gupta, Chemical Products Director at WSS, and, like his colleague Ostlund, an expert in marine fuel matters.
"Distillate fuel contains paraffins, or wax particles, and colder climates pull these together to create large structures. These structures, basically waxy sludge masses, accumulate in fuel tanks and block fuel filters, damaging them and causing an increasing number of loss of power (LOP) incidents.
"This is an obvious technical and safety concern for all vessels,” he stresses, “and one that must be addressed.”
Cutting through the confusion
The increased take-up of low sulphur distillate fuels, and the growing number of LOPs, is creating greater awareness of the wax issue. However, the industry's understanding of it remains as opaque as the affected fuels themselves.
"It is complex,” Ostlund admits, “and that creates confusion. A key issue is that fuels with only slight differences of the same grade can react very differently at cold temperatures – with some flowing freely, while others have catastrophic effects on fuel filters. It's therefore vital to have a clear picture of both the temperatures vessels will be operating in and the characteristics, quality and specifications of the fuel you intend to use.”
Ostlund and Gupta note that there are three measurable stages related to wax formation in distillates that should help owners and operators make informed choices.
It is vital, they say, to be aware of these and know the exact temperature at which a fuel will enter the first two of these three phases.
Cloud Point (CP)
CP is the point when the wax particles that have formed actually become visible, causing a clouding or hazing in the fuel (ISO 3015).
"The CP should act as the first and final warning,” Gupta stresses, “as it gives a very clear indication that action has to be taken.”
But, as he admits, that's not always as simple as it sounds: “Warnings are only effective if they're seen. When fuel is enclosed in tanks it's not always easy to notice the clouding, so, if there’s any confusion over the CP, crews have to visibly check fuel on a regular basis.”
Cold Filter Plugging Point (CFPP)
"CFPP is the point of no return,” says Ostlund matter-of-factly, going on to explain that the standard is set by analysing the exact temperature at which a set volume of fuel fails to pass through a 45-micron filter within 60 seconds (ASTM D6371). “It effectively marks the temperature at which the build up of wax crystals stops fuel from passing through the filter. Starved of fuel the engine stops, leaving vessels with few alternatives and, quite literally, nowhere to go.”
Pour Point (PP)
"Pour Point is arguably the least useful of the three measures, as it indicates the temperature at which fuel turns solid (ISO 3016),” Gupta comments. “That means that a vessel's engines would have stopped operating before the PP is reached. That said, it is the only measure that is required by ISO8217 fuel specifications, so it is important. But for crews and bunker brokers, it's the CP and CFPP they need to focus on.”
As a point of interest, Gupta adds that the difference in temperature between the CFPP and PP is typically only between 5 and 10 degrees.
Avoiding sticky situations
The relative immaturity of the marriage between ECA and fuel distillates is causing genuine teething troubles, as the industry adjusts to the fuel and its, some might say, capricious character. WSS notes that filter issues and LOPs are a real concern, rather than just the latest industry scare story, and one that is growing all the time.
"But follow some simple rules and these problems can be avoided,” asserts Ostlund.
He says that knowing projected operating temperatures at sea will inform decisions on the required cold flow properties of potential distillate fuels, with CP and CFPP used as the key metrics.
"If you are unsure, hedge your bets, buy distillates designed for slightly colder waters than your vessels are likely to be sailing in,” he advises, adding:
"In addition to ensuring crews know pre-determined CP and CFPP figures for the distillate in use, shipping firms also need to make sure they are familiar with using sounding tape and a sounding pipe to measure and analyse the condition of fuel. Although this is a rather crude method of assessing fuel, it is the only quick and convenient solution, due to the fact that it's otherwise difficult to visually check fuel that is enclosed in bunker tanks.
"This kind of disciplined, well-informed approach really is the foundation for trouble-free sailing.”
Keeping help at hand
That foundation can be built upon, strengthening operational integrity, with one more simple action – the routine use of distillate fuel treatments.
Gupta describes this additive as an “extra buffer”, explaining: “Distillate fuel treatments don’t have any impact upon the Cloud Point, but both the CFPP and PP can be extended by the use of cold flow additives. This postpones the formation of wax crystals giving breathing space in terms of both operations and man-hours, reducing the need for constant, close monitoring of tank and fuel temperatures.”
He continues: “ISO 8217 limits the cold flow properties of a fuel by setting a limit on the pour point (PP). However, given that wax crystals form at temperatures above the PP – and can rapidly block filters - fuels that meet PP specification can still be problematic for operations in colder regions. For example, there are industry cases where onboard fuel PP has been -6C, but waxy sludge has formed at temperatures as high as 16C!”
WSS markets its own Unitor DieselPower distillate fuel treatment range, with DieselPower CFPP a proven solution for vastly improving the cold flow properties of distillates.
"It contains a unique mixture of cold flow improvers,” Gupta states, “together with a wax anti settling additive (WASA), to ensure no sediment is formed. It's simple to use, being added prior to the filling of fuel tanks, and is dosed one litre to one thousand litres of fuel.
"This kind of treatment represent a minimal cost for maximum peace of mind when it comes to cold climate operations. They can help keep vessels safe when temperatures approach the limits of what a fuel can tolerate and should, along with knowledge of CP, CFPP and projected operating temperatures, become second nature within engine rooms.
"Prevention of this waxy sludge is much easier than finding a cure,” he concludes - something that everyone struggling with a winter cold will no doubt agree with.
Paraffin precautions
Paraffins, or alkanes, are an essential component of petroleum fuel products, offering good combustion properties and burning well within engines. However, exposure to low temperatures can cause crystallisation, leading to blockages of vessel fuel filters and potential engine shut downs. Knowledge of marine fuel cold flow properties, sound on-board procedures, and additional measures, such as adding specialised treatments to fuel distillates, can help vessels avoid these serious operational issues.
When in doubt
Always consider 'worst case' CFPP and PP properties and characteristics. Assess current and future trading patterns for vessels, and potential sea and ambient temperatures, and err on the side of caution. As a rule of thumb, always choose distillate fuels that are suitable for slightly colder waters than those where your ships will be sailing.
For further guidance see CIMAC's 'cold flow properties of marine fuel oils'.