Digital rope management with all-in-one LMP application
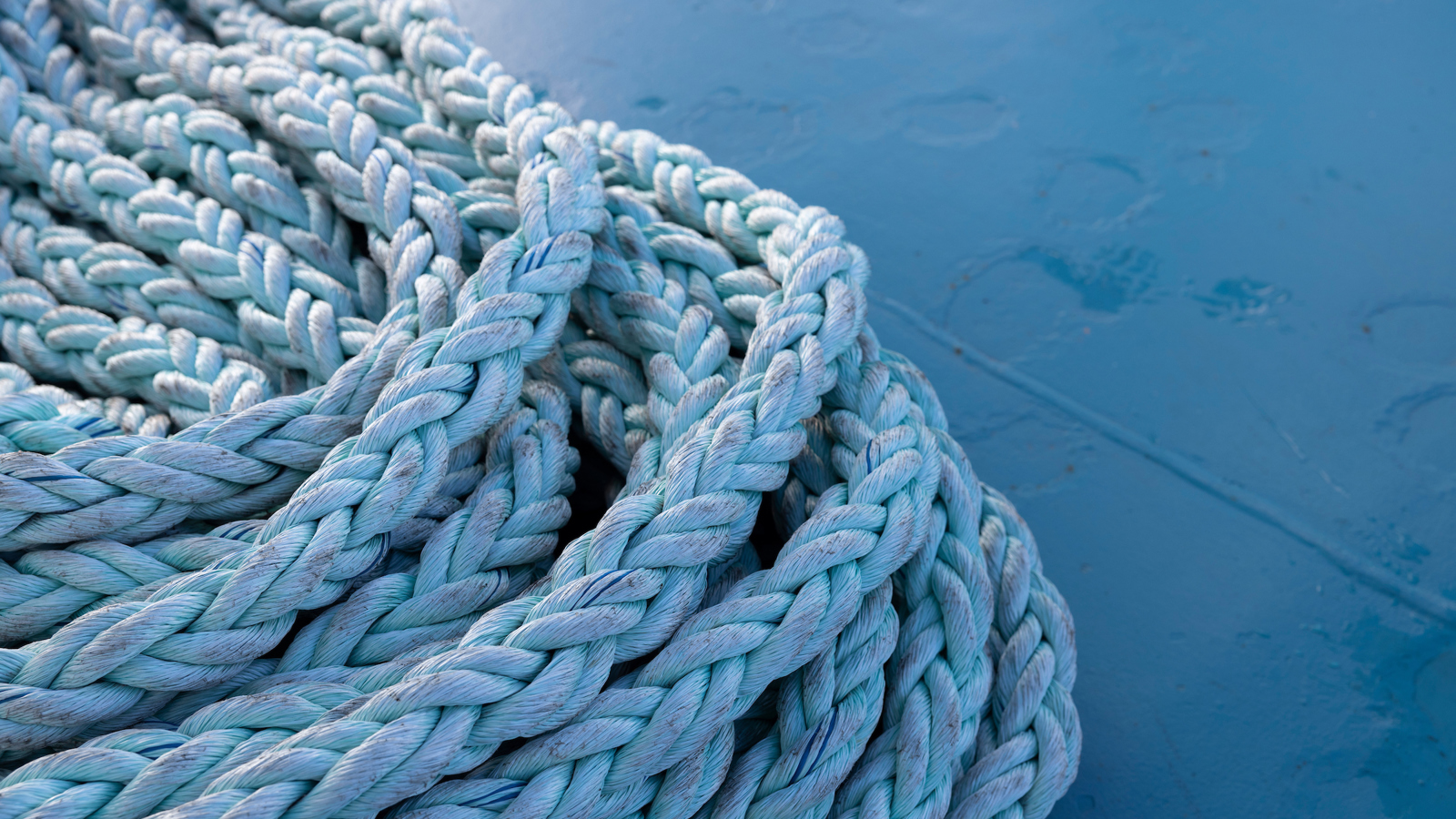
Wilhelmsen insights
|
Ingvild Beldring, Digital Product Manager
The regulatory framework
Implementation of an LMP, providing updated information about how lines are used and maintained to avoid accidents, is a critical element in existing regulations related to rope management.
Leading the way among the regulations is the Oil Companies International Marine Forum Mooring Equipment Guidelines (OCIMF MEG4), which provide recommendations for the safe mooring of tankers and LNG carriers.
OCIMF MEG4 sets the foundation for a much-needed system of support tools. The LMP forms part of the Mooring System Management Plan, which is designed to ensure that the entire mooring system is inspected, maintained and operated in accordance with the original vessel design.
Inspection regimes
The OCIMF Ship Inspection Report Programme (OCIMF SIRE 2.0) being rolled out this year utilizes many of the key OCIMF MEG4 concepts in its questionnaires, including a strong focus on the LMP. Trade association Intertanko has also adopted the OCIMF MEG4 recommendations.
In the dry bulk segment, the RightShip Inspection Ship Questionnaire (RISQ), which is applicable primarily to bulk carriers, general cargo ships and containerships, also employs many OCIMF MEG 4 requirements in its section on mooring lines, including the implementation of an LMP.
Soon to be mandatory
From 1 January 2024, following the new IMO Safety of Life at Sea (SOLAS) MSC.1/Circ. 1620 regulation, all vessels will be required to have an LMP in place.
To be compliant, the LMP should contain information including records of mooring hours, line test/inspection plans, records and reports, manufacturer and operator retirement criteria, manufacturer's recommendations following tests or inspections, and wear zone management. Users should also be able to identify the location of lines (either loose or which line is connected to which winch), relevant documents including certificates, and how ropes are stowed.
An LMP can take different forms, from paper-based or electronic documents to dedicated software. However, both OCIMF MEG4 and RISQ indicate the LMP should be capable of being updated and easy to access from a single location for both onboard and shore personnel – which strongly implies that the best solution is digital.
Emphasis on user-friendliness
LMP™ by Wilhelmsen is a cloud-based application that provides a complete digital logbook, so you always have the latest data to hand. Along with easy-to-use manuals and support for crew members, we put a lot of effort into making the user experience as intuitive as possible. The subscription-based system works seamlessly across PCs and handheld devices and is fast and easy to start using – the average implementation time on a new vessel, including training users, is less than an hour.
Easily accessible for both shore and ship personnel, our LMP provides a single place to store all your rope certificates and get an immediate overview of your inventory – where your ropes are currently located, their mooring hours from every port call, and latest and upcoming inspections.
It is easy to register rules and criteria in the app, such as when to inspect a rope, when to turn lines end-to-end, when to relocate and when to retire lines, and get notified when these actions are applied. You can also extract all relevant mooring and line data in tailored reports.
LMP™ by Wilhelmsen
Compliance made easy
Our LMP helps to reduce complexity by replacing messy fragmented solutions with a single online system; no more fiddling around with Excel spreadsheets. That means you save time and effort while enabling opportunities to effectively track, compare and optimize the complete lifecycle of your ropes across multiple vessels. In the event of a mooring-related incident, having the correct documentation and system in place can make the difference between a prolonged stay in port or a quick turnaround.
The risks of non-compliance
Most importantly, non-compliance with regulations can potentially create unsafe situations and lead to accidents, so ensuring compliance is the best way to safeguard the wellbeing of both your crew and workers on the quayside. A further consequence is that non-conformities observed during external inspections will require the ship operator to implement suitable remedial action, which may result in additional costs, downtime and reputational damage. Note that vessels having a high number of non-conformities may be less likely to secure valuable charter business.
The average duration of a RightShip RISQ inspection is close to 15 hours, with an average of 22 non-conformities across all vessels. The inspection is not only time-consuming but corrective action may also result in delays that can impact costs further.
Implementing a well-maintained and exhaustive LMP, periodic inspection procedures and keeping mooring lines in good condition will ensure compliance and reduce the time used on inspections and addressing problem issues.
LMP functionalities address key pain points
There are several challenges associated with rope management that our LMP functionalities conveniently solve.
Keeping a handle on rope certificates, for example, has always been a headache in the analog world. Crews can have a hard time locating all certificates in the first place, then have difficulty knowing for certain what certificate belongs to what rope. Misplaced certificates saved as hard copies onboard can be exacerbated by the fact that crews can and do change.
Line location made easy
Remembering for certain which line is on which winch can also be confusing, especially if the line is not clearly tagged or labelled. Always updating our LMP when you move a line in real life means you always keep track of which line is where.
If you move a line to a new location (for example, between winches or moving a line from a winch to loose stowage), our LMP accurately stores that history along with the date so you can always see where each line has been previously. This makes it possible to investigate what locations on your vessel could be more damaging or cause more tension on the lines, so that in the future you can take preventative action.
Inspection page with examples
We also understand that it is difficult for the crew to know both what type of damage is on a line as well as the severity of damage. The inspection page in our LMP provides a long list of examples of damage, and for each damage we there is a descriptive text along with photos showing three grades of severity. This gives the crew the possibility to compare the line they are inspecting with examples in our retirement guidelines.
Having updated data that is streamlined across your fleet – with our LMP the records of rope management are not fragmented and reported differently for each vessel, the data is streamlined and easy to read.
Unmatched fleet insight
Another major advantage of our LMP is the Fleet Overview function providing vessel/fleet managers with rope management data across their fleet. They no longer have to read individual reports or chase documents from vessels – they get everything in one user-friendly dashboard that is continuously supported and updated with live data from each vessel. And instead of listing all the data and the user having to figure it out themselves, we give insights into what is needed to take action on and what issues require attention. This makes it easy to assess the performance of rope management across vessels as well as proactively plan for rope retirement and centralized product procurement.
Condition monitoring using AI
We are constantly looking at ways to add value, and as part of our LMP development we are currently building a computer-vision tool that can give feedback on the condition of ropes simply by analyzing photos. The model has been trained on thousands of pictures of ropes classified according to their condition (good, medium or poor). This means that when crew members perform inspections, they can upload a photo of a particular rope and get an immediate response on its condition based on the learned dataset. The tool is designed to reinforce the confidence of seafarers, ensure that ropes that should be retired are not still in use and those that still have more life in them are not retired too early. You can also avoid accidents by ensuring your crew are trained in detecting conditions and working with ropes that are safe to use.