How flashback arrestors keep maritime gas welding and cutting safe
Wilhelmsen insights
|
Chris Teoh, Senior Product Manager – Welding & Repair
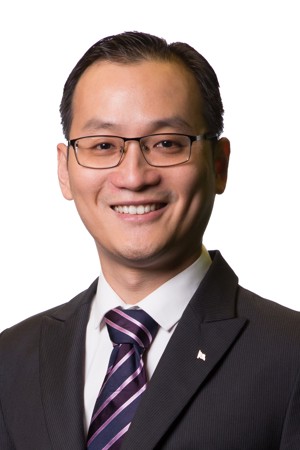
Oxy-acetylene torches have been a staple in the maritime industry for many decades and are used for metal cutting, welding, brazing and heating during onboard maintenance. When purchasing gas welding and cutting equipment, one often overlooked aspect is ensuring that the equipment meets technical specifications for safety and compliance. By investing in good-quality equipment that adheres to strict safety standard requirements, you can significantly reduce the risk of fire and explosions onboard.
Despite close attention paid to gas welding and cutting safety, there are still too many cases of personnel being injured or even killed due to the use of poor or substandard quality equipment. There have been incidents where flashback into acetylene cylinders has triggered decomposition of the gas causing the cylinder to explode. In one case, a cylinder exploded only three minutes after a flashback with devastating results (see Figure 1). Fortunately, no one was injured because the operator realized that the cylinder was in a dangerous condition, raised the alarm and the location was evacuated (Reference: AIGA Safety Bulletin 01/05).
Figure 1: Oxy-acetylene gas cylinders that caught fire and exploded in a flashback arrestor incident where the fire travelled through the hose and directly into the gas cylinders. Source: https://safety.army.mil/ON-DUTY/Workplace/
Protecting against flashbacks during hot work is in line with the International Safety Management (ISM) Code and the Maritime Labour Convention (MLC) 2006, under which ship owners and operators are obliged to do their utmost to safeguard the occupational health and safety of personnel and prevent accidents both at sea and in ports.
Awareness is everything in ensuring the right behaviour. In a recent Welding Safety Inspection (WSI), for instance, our inspector discovered that flashback arrestors were missing from the gas welding and cutting equipment, where the consequences in the event of a flashback accident could be severe and disastrous. A strong safety culture and the right mindset among crew members are essential for reducing safety risks.
Flashbacks explained
Under correct conditions, where there is a balance between the gas mix exit velocity (i.e., speed of the gas out of the nozzle) and the combustion velocity (i.e., burning speed of the gas), the gas will burn correctly in a stable manner. A flashback will occur if the combustion velocity exceeds the gas mix exit velocity, with the flame burning into the equipment. Flashbacks typically occur at the cutting nozzle or welding attachment tip (orifice) of the torch setup.
Typically, flashbacks can be attributed to either human factors or equipment / environment factors below:
Human Factors | Equipment / Environment Factors |
|
|
What to do in the unlikely event of a flashback
Acetylene is extremely flammable, unstable and under certain conditions can decompose explosively into its constituent elements, carbon and hydrogen. A flashback can trigger decomposition in the acetylene cylinder. Therefore, it is crucial to keep the cylinder on the uppermost continuous deck and ensure direct access to the open deck. This allows for easy removal in case of an emergency. Never keep cylinders inside the hull. Note that UnitorTM acetylene cylinders are designed in line with international standards, incorporating features that allow for safe filling and storage of acetylene gas, and retard any acetylene decomposition should it occur, providing enough time for emergency actions to be taken.
If a flashback occurs and it is safe to do so, immediately close both acetylene and oxygen cylinder valves. The flame should go out when the acetylene is shut off. If the flame cannot be extinguished at once, evacuate the area. It is important to keep mittens or gloves in a convenient location near to the gas cylinder. The mittens or gloves should be made from flame-retardant material and can be used on either hand to close the top valve of an acetylene cylinder that is on fire.
Carefully check the cylinder and any other acetylene cylinders that may have been affected by fire or flames. If the cylinder becomes more than hand warm (60-70°C) or starts to vibrate, evacuate the location immediately. Do not attempt to move an unstable cylinder; moving it could restart or accelerate the gas decomposition. It could be several days before it can be moved. Use the fire hose from a distance of at least 20m and hose down the cylinder body with a direct water spray. Cooling the cylinder down is the only way to stop decomposition.
Depending on the situation, throw the cylinder overboard.
What should you look for when purchasing flashback arrestors?
Despite welding equipment being a low investment priority versus, for example, fuel costs, it is important to embed the right behaviours among your personnel to decrease the likelihood of incidents. Safety is paramount. Replace expired products (in terms of life expectancy, arrestors should be replaced every five years in line with OCIMF SIRE 2.0 or RightShip RISQ 2.0/3.0 requirements) and only purchase flashback arrestors manufactured to the ISO 5175-1 standard and that have BAM (Bundesanstalt für Materialforschung und -prüfung or German Federal Institute for Materials Research and Testing) certification and under-surveillance approvals.
The key selection criterium is to only buy flashback arrestors from a trusted source or reputable manufacturer with a good safety track record. Avoid buying second-hand units, incorrect type or flashback arrestors with no local standards.
Wilhelmsen Ships Service (WSS) has been supplying high-quality UnitorTM gas equipment for decades with an excellent safety track record in the maritime industry. All our flashback arrestors provide reliable protection against dangerous reverse gas flow and flashbacks according to EN ISO 5175-1. Our 85-10 series, S- 55 and W-66S products are BAM certified, while our basic FR-20 product conforms to EN ISO 5175-1 and are all manufactured by an industry leading manufacturer and subjected to rigorous testing.
Figure 2: Unitor Flashback arrestor range and applications
Weld safely with us
It pays to be fully aware of all the safety hazards relating to hot work onboard vessels, ensuring that all your welding and cutting equipment is shipshape. Independent inspections by a third party can verify that you are up to scratch. We see many customers returning to us having had negative experiences using, for example, low-pressure injection equipment, which we believe is inherently much less safe than our solution.
We also offer industry-leading Welding Safety Inspections where we will immediately highlight urgent issues including the absence or expired flashback arrestors. You can also take advantage of UnitorTM welding training courses at our welding schools so your crew is fully up to speed on the latest cutting and welding techniques and safety parameters.
With WSS you are in the best hands. Unitor – improving safety, optimising performance.