Fuel Treatment: Efficiency gains more than just hot air
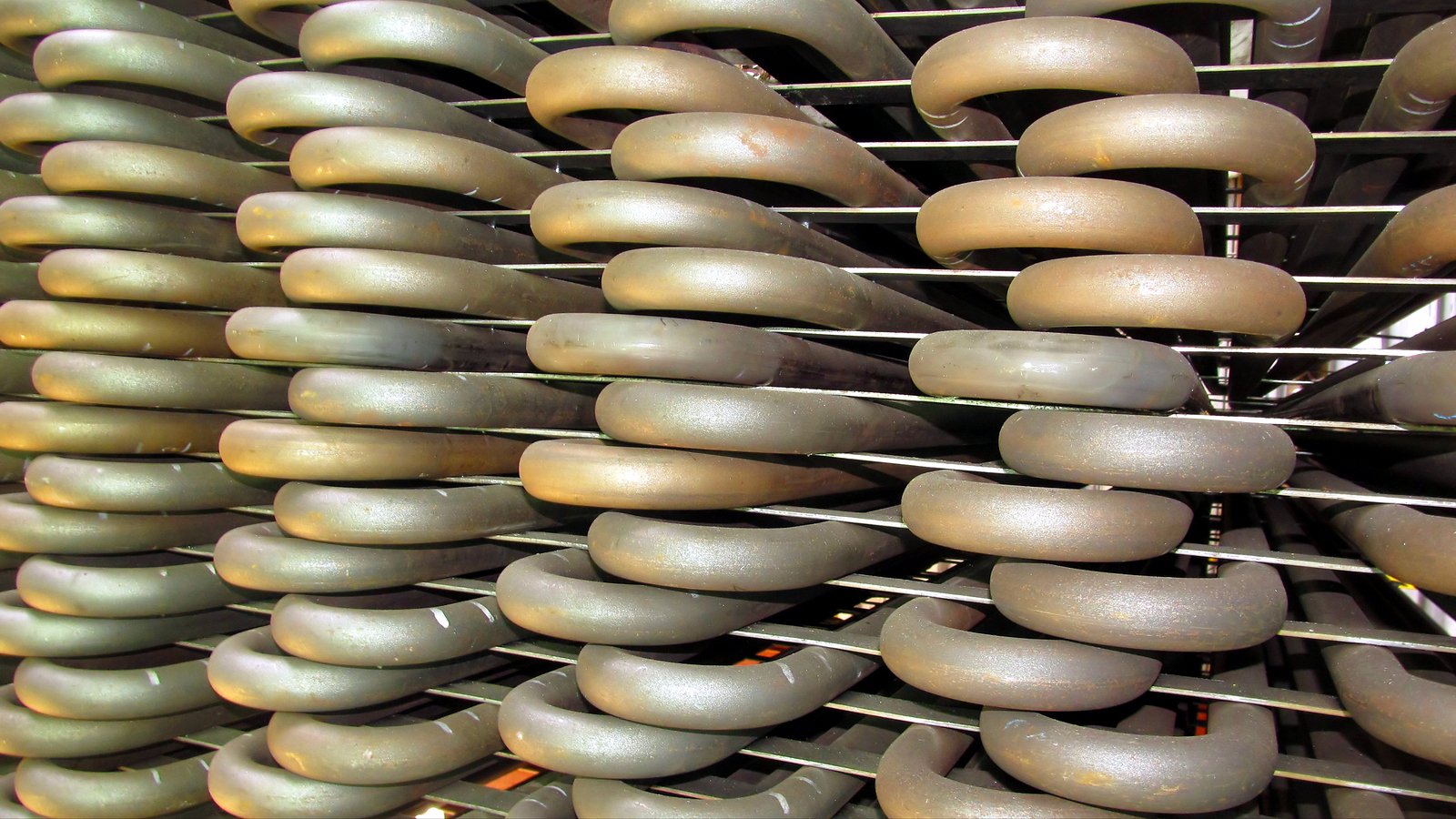
Wilhelmsen insights
|
Jonas Östlund, Head of Product Management - Energy Solutions
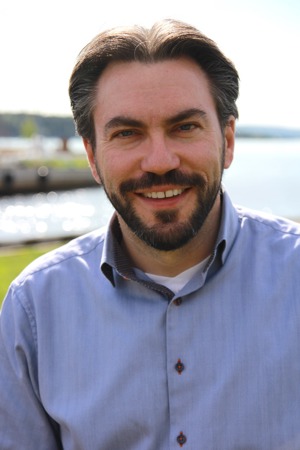
Lubricity, biocide and stabilizer treatment products have rightly become part of a vessel’s fuel management routine, but many operators have yet to recognize the value of intervention, post-combustion. Fuel treatment shouldn’t end in the fuel tanks, there are still issues unique to residual fuels which need to be faced further along the line.
Soot for everyone! – The mechanics of exhaust gas boiler build-up
Burning today’s heavy fuels can be a challenge due to the quality of the fuel. The refining process leaves residual fuels full of contaminants and after cutting with a diluent, heavy fuels have a tendency to become unstable or incompatible. Fuel becomes a challenge to burn completely and the ash contaminates in the fuel such as Asphalt, Vanadium, Sodium, Aluminium, Silica, and Potassium cause deposits. Sometimes forming on exhaust gas valves and the turbo charger nozzle, these deposits are however temperature dependent. The ignition temperature of such soot or carbon particles is high typically around 600°C. Therefore, particles typically pass both the exhaust valves and the turbo charger and continue with the flue gases until they reach the exhaust gas boiler (EGB).
Challenges with efficient design and slow steaming
New engine designs focusing on increased thermal efficiency have resulted in lower exhaust gas temperatures. Exhaust gas temperatures can range from 220°C to 270°C and coupled with today’s slow steaming practices, the exhaust gas temp can drop as low as 180°C. Such low temperatures result in unburnt wet soot sticking to EGB surfaces, causing corrosion and potentially causing fires. As the particle cools, while entering the boiler, it becomes wet with either oil or condensate from hydrocarbons and highly adhesive, sticking to the heat transfer surfaces of the boiler.
As modern thermally efficient EGB’s are designed to incorporate large heat transfer surfaces when working with such low speeds soot is able to deposit more readily. Once in place, the soot obstruction then increases the pressure difference over the exhaust gas boiler and this further lowers exhaust gas velocities below acceptable levels.
At the specified Maximum Continuous Rating (MCR) of the engine, the maximum recommended pressure loss across the exhaust gas boiler is normally 150mm WC. This pressure loss depends on the pressure loss in the rest of the system. Therefore, if an exhaust gas silencer/spark arrester is not installed, the acceptable pressure loss across the boiler may be somewhat higher than the maximum of 150mm WC. If an exhaust gas silencer/ spark arrester is installed, it may be necessary to reduce the maximum pressure loss.
Now it is time for the engine room to find several hours during their next port call to clean the EGB.
When an inconvenience becomes a major problem
Untreated flue gases soil the EGB, which then requires cleaning, typically every second or third month. So what you might say? It is a minor hassle at worst.
Well yes, and no. Performed in port, a decent cleaning job takes approximately five hours, will of course require labour and equipment and also demand fresh water from the vessel for final rinsing and wash. In addition, discharging the dirty wash water is easier said, than done. Containing acidic soot how such waste should be managed is still a question awaiting regulatory guidance.
Two meetings ago the MEPC (Marine Environment Protection Committee) aimed to provide clarification and to present a change in Annex V of the MARPOL regulation. The intention being to include the wastewater from exhaust gas boiler cleaning within the garbage regs. However, this hasn’t happened and there are still no formal guidelines on how to discharge the waste with practises differing depending on the systems on board. A regulatory work in progress, the indication is that wastewater will have to be sent ashore for disposal.
While recognising the extra work and costs associated with cleaning, operators should look at the bigger, sootier picture. Sadly, labour and disposal costs are just the beginning of the bad news, it gets much worse as soot deposits can reduce the efficiency of the EGB and if left unchecked permanently damage it.
A 1mm layer of soot can reduce exhaust gas boiler efficiency by 10%. Left to build up to a 3mm layer, EGB efficiency can be reduced by up to 50%.
Reducing efficiency one millimetre at a time
Just like any heat exchanger, any deposit will reduce the transfer of heat and therefore reduce the efficiency of the equipment.Soot deposits are particularly effective at reducing heat transfer as they are extremely insulating. Offering a similar level of insulation as rock wool, used in home construction, a 1mm layer of soot can reduce exhaust gas boiler efficiency by 10%. Left to build up to a 3mm layer EGB efficiency can be reduced by up to 50%.
Catch fire
The most common design for EGB is a water tube type boiler utilizing the stream drum of the oil-fired boiler. An efficient and compact design it includes an expanded heat transfer area incorporating narrowly spaced, gilled (finned) or pinned tubes. Believed to have dramatically reduced the possibility of soot build-up and the potential for soot fires, these new designs can actually promote the accumulation of soot.
The clearance between the gill-type fins (face-to-face) is typically 10-13 mm and the thickness of the gills is about 2-3 mm. Such tight clearances between heat transfer surfaces allows the build-up of deposits on the upper side of the EGB tube. Cleaning by steam blowing is not sufficient and as mentioned above, the lower speed of exhaust gas only escalates the problem. In extreme cases, if unchecked, soot deposits can lead to soot fires causing permanent damage to the EGB.
The reason such fires can occur is while the main component of soot deposits is particulates, unburnt fuel and lubricating oil residue can also be deposited in the boiler. Unburnt fuel lowers the ignition temperature of the soot layer significantly from 300-400°C way down to 150°C which when combined with low exhaust gas velocities and/or low water circulation creates the ideal conditions for soot deposits to ignite. While the frequency of soot fires has no doubt decreased over the last decade, because of improved exhaust gas boiler designs, as highlighted by classification society DNV, they nevertheless do still pose a threat.
Cold corrosion
If the prospect of fire was not daunting enough, another unwanted issue, which can occur with EGBs operating at low velocities, is cold acid corrosion.
Caused by the sulphur content of the fuel reacting with oxygen during combustion, this chemical reaction forms Sulphur dioxide and Sulphur Trioxide. When the temperature drops below 135°C (275°F) the Sulphur Trioxide reacts with the moisture in the air and forms sulphuric acid.
Today’s EGB’s demand low evaporation or exhaust temperatures in order to generate the required steam pressure, so are designed to drastically reduce the temperature by so efficiently removing heat from the exhaust gas. Ultimately, they help produce the ideal conditions for the creation of sulphuric acid condensation.
With a pH value below 1, sulphuric acid is very corrosive to tube surfaces and corrodes metals in a similar way to rust. It is therefore important to keep the circulation and feed water temperature in the tubes above 135°C to keep corrosion at bay.
- at fuel combustion: S + O2 = SO2
- at cooling of exhaust gas in the temperature range of 560° - 200°C: 2SO2 + O2 = 2SO3
- at reaction with water: SO3 + H2O = H2SO4
Minimal investment, significant gains
Whether it is operational challenges, such as regular boiler cleaning and waste discharge, or equipment issues including reduced EGB efficiency, soot fires and cold corrosion, preventative measures are available which can eliminate many of the challenges flue gases can pose.
For example, Unitor’s FuelPower Soot Remover Liquid Plus from Wilhelmsen’s innovative fuel treatment range is one such product. Dosed four times a day and sprayed as a very fine mist it condensates onto the soot continuing to oxidize it, meaning almost no soot is actually deposited in the exhaust gas boiler. Active from 180°C it is also suitable for the range of low exhaust gas temperatures associated with slow steaming.
With minimal deposits on the exhaust gas boiler, cleaning will only need to be performed just once a year, rather than every other month. Promoting greater fuel efficiency and helping to minimize the risk of soot fires, Soot Remover Plus also prevents acid formation in areas where severe corrosion could result in expensive damage, i.e. heat exchangers, super heaters, economisers and exhaust paths/stacks.
A relatively new area of fuel treatment, while some may be sceptical about the benefits additives offer and of course wary to yet more add-on costs, this treatment is essential - the cost, which is less than half a percent of the daily fuel cost per day, really is a negligible outlay when measured against the very real efficiency gains fuel treatment is proven to offer.
Your "Magic Potion" is still working wonders and except for some light dust on top it all looks practically clean even though we lately have been using only 40% on the pump.
Stein Gravdal, Chief Engineer, M/V Tønsberg
Tested in the lab, proven at sea
Developing and producing our own marine chemicals at our Wilhelmsen Chemicals facility located in Tønsberg, Norway, while laboratory testing can provide key indicators on a product’s performance it is at sea where chemicals prove their true worth.
Trialled for the past year aboard the RoRo carrier MV Tønsberg the performance, and indeed value, of products such as Soot Remover Plus is as clear as the inside of their ECB.
Owned and operated by our sister company Wilh.Wilhelmsen the 76,500 GT RoRo is equipped with a MAN B&W 7 Cylinder L70 ME-C8 main engine. An ideal test candidate, the vessel has a regular trading pattern between Europe, the US and Japan and their exhaust gas boiler requires regular cleaning, every two months.
The trial began by cleaning the exhaust gas boiler and installing the automatic dosing unit. It is important to clean the exhaust gas boiler before stating the trial as the product will keep the boiler clean, but will not clean up deposits already in the exhaust gas boiler. Dosing four times per day at 6-hour intervals, following progress closely, we received reports from the vessel at every port call and visited the vessel three times during the trial. The results are impressive to say the least.
At the last ECB inspection, the vessel had been sailing for ten months without needing to clean the exhaust gas boiler. Not once. The Chief Engineer is satisfied with the performance of product and the stability of the TG output indicates a clean Economiser.
Cynics may question the validity of test conducted aboard one of ‘our’ vessels. However, anyone with a passing knowledge of W.W’s business will acknowledge that their operations are driven by the single-minded pursuit of efficiency gains and improved performance, rather than sentiment.
Dosing Details
Dosing
The dosing for the trial was decided by the fuel consumption of the vessel. The fuel burned produces a certain amount of flue gas that needs to be treated. The trial vessel consumes about 60 tons of fuel per day so the dosage for the trial was set at 5.38 litres per day. The dosing unit was set for 50% stroke that is equal to 5.38 Litre per day.
Dosing Unit
Power |
120-230 VAC, 50/60Hz, 40VA max |
Air Supply |
7 bar nominal (5 bar min to 8 bar max) |
Dimensions |
400 (w) x 800 (h) x 400 (d) mm |
Weight |
10 kg |
The Science of Soot Removal
FuelPower Soot Remover Liquid Plus contains diesel oxidation catalysts made up of catalytic converters. Therefore, as the hot gases contact the catalyst the exhaust pollutants are converted into harmless substances, carbon dioxide and water.
The Chemical reaction is:
- CO + ½ O22 àCO 2
- (Hydrocarbons) + O2 àCO2 + H2O
- (SOF) + O2 àCO2 + H2O
Note: The remaining dry, solid carbon particles do not stick to surfaces and follow the exhaust gas.
EGB Cleaning – Best Practice
Regardless of the frequency your boiler needs to be cleaned, dependent of course on if your fuel is treated or not, there are some basic step-by-step cleaning guidelines you should follow.
- Shut down boiler and allow unit to cool.
- Water wash using a hand held hose or lance. Salt water may be used for initial washing although fresh water is preferable, usual quantity in the region of 15 – 20 tons. To aid the removal of acidic soot deposits, a mildly neutralising detergent may be added to the water wash. For mild cleaning a product such as Unitor’s Aquabreak PX is ideal.
- If fouling is severe and deposits are difficult to remove, it may be necessary to apply chemical detergent solutions directly to the tube surfaces prior to washing. Allow time to soak before hosing down. For cleaning of severe deposits we recommend a product such as Unitor’s Aquatuff*.
- Final rinsing of tubes should be at least 30 minutes with fresh water to remove all salt water if used and/or cleaning chemicals.
*If necessary use 0.5 liter of Defoamer Concentrate to each pail of Aquatuff to avoid excessive production of foam.
Discharge of Wastewater and Soot
The majority of vessels are fitted with a soot collection tank for soot/wash retention while water washing exhaust gas boilers or economisers.
Some designs have the soot discharged directly overboard via an educator driven by the fire main or similar arrangement. Others are a simple collection tank and ‘weir system’ wherein the soot is retained within the tank with wash water returning to bilge for discharge overboard via the OWS. Of course the approved plans for the vessel’s arrangements should be on-board.
With regard to the ‘weir system’ the soot is then collected and retained on-board for disposal ashore. Whenever soot is landed ashore for disposal, pertinent details should be recorded in the Garbage Log Book.
Learn more about oil solutions
Download "Efficiency gains more than just hot air" white paper