Aim Zero: Towards zero harm from hot work at sea
Wilhelmsen insights
|
Chris Teoh, Senior Product Manager – Welding & Repair
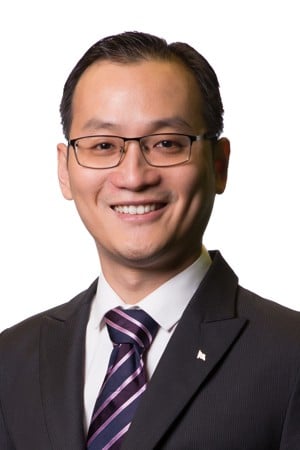
In the complex world of maritime operations, hot work — welding, cutting, heating and grinding — represents one of the most hazardous activities performed onboard vessels. Despite decades of awareness campaigns, regulations and safety innovations, hot work remains one of the leading causes of shipboard fires, explosions and fatalities.
THE PERSISTENT RISKS ASSOCIATED WITH HOT WORK AT SEA
The harsh reality is that fires linked to hot work accidents continue to occur with alarming regularity, often resulting in severe financial losses, damage to vessels and injuries and even loss of life. According to marine insurance provider Gard, based on their 2014-2024 claims data, hot work related fires frequently occur in pump rooms, cargo tanks, holds, and machinery spaces. Nearly 60% of related insurance claims fall under Hull & Machinery insurance, and 40% under P&I insurance – covering cargo loss, personnel injuries, and third-party liabilities.
Figure 1: Vessel engine room
To address these risks, Wilhelmsen Ships Service (WSS) has launched Aim Zero, a holistic hot work safety campaign with a vision to achieve zero deficiencies, zero incidents, zero losses and zero harm. Aim Zero isn't just about checking boxes; it's about building a proactive safety culture onboard ships, empowering seafarers to take ownership of safety from shipyard to the high seas.
RISKS OF HOT WORK – A CLOSER LOOK
Hot work introduces multiple risks, including:
Hazard |
Causes |
Consequences |
Fire & explosion | Sparks, heat transfer, gas leaks, flashback fire | Vessel loss, structural damage, injury/fatality, pollution |
Electric shock / electrocution | Non-compliant welding machines, exposed insulation, improper grounding | Severe injuries, including burns, muscle paralysis or fatality |
THE REGULATORY LANDSCAPE: A LONG HISTORY OF WARNINGS
Hot work safety regulation is nothing new. In the maritime context, the International Safety Guide for Oil Tankers and Terminals (ISGOTT) first addressed it in 1978, with additional emphasis given in the 1999 UK Code of Safe Working Practices for Merchant Seafarers (COSWP) and various other publications. COSWP emphasized safety guidelines for hot work including permit-to-work systems, risk assessments and procedural controls.
However, adherence to these guidelines remained patchy, and it is only in the last decade that vetting programs like OCIMF SIRE 2.0 (for tankers) and Rightship RISQ 3.1 (for bulkers) have incorporated hot work safety requirements into their inspection protocols. These latest updates have required operators to improve equipment, processes and training – transforming hot work safety from a 'nice to have' to a 'must have'.
In practice, however, hot work safety is often overlooked unless triggered by incidents or inspections. For example, RightShip RISQ inspection findings for 2024 revealed 1,265 hot work safety instances – or a finding ratio of 38% across a total of 3,309 inspections – down from a finding ratio in 2023 of 59%. Although this shows a positive improvement for hot work safety, it remains a high-attention point given the continued high numbers of findings.
Figure 2: WSS Port Service Engineer carrying out a Welding Safety Inspection
As regards Port State Control (PSC) inspections, which are of course extremely thorough, due to their enormous scope they may tend to focus on or prioritize critical factors such as navigation safety, water/weathertight conditions, emergency systems, fire safety, lifesaving appliances, etc. While hot work safety is one of the 10 Golden Safety Rules recognized by the maritime industry – requiring focused attention to prevent accidents and ensure the safety and well-being of seafarers – inspections may sometimes miss less obvious issues than those that are clearly observable.
These might include, for example, non-compliant welding machines with high Open Circuit Voltage (OCV), missing non-return valves on gas cutting and welding torches, or the condition of the welding fume extraction unit.
AIM ZERO: MOVING BEYOND COMPLIANCE TO SAFETY CULTURE
The core purpose of Aim Zero is to embed a culture of proactive safety ownership. Regulations alone are not enough. True safety comes from a holistic approach that considers people, equipment, materials, processes and performance monitoring — encapsulated in the 5M framework:
MAN – Competence and Safety Mindset Matter Most
- Human error contributes to 70-80% of maritime incidents.
- Aim Zero promotes continuous training for seafarers through Unitor™ Welding Schools, emphasizing hot work safety, safe equipment handling and practical welding skills.
- AimZero also supports the behavioural shift – whereby vetting inspectors no longer accept a completed checklist only but instead interview crew to assess their real-world understanding of safe practices.
MACHINE – Safety by Design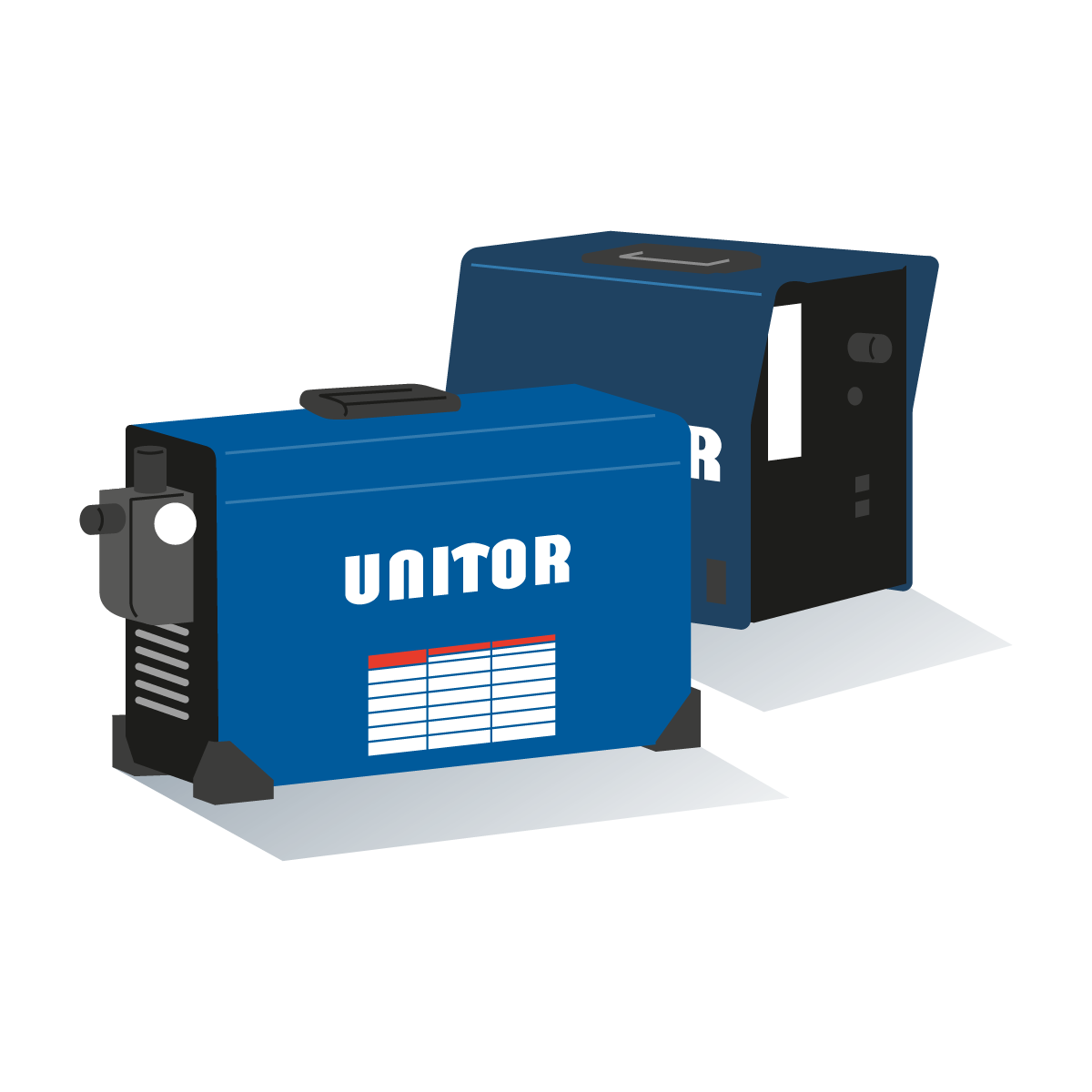
- Aim Zero promotes the use of certified and compliant, high-quality welding and cutting equipment – sourced correctly during newbuild construction to avoid costly retrofits or replacements.
- Shipyard-supplied equipment from land-based suppliers can often fail to meet maritime safety standards, leaving operators exposed after delivery. Rather than focusing on cost over safety, Aim Zero encourages operators to ‘Get It Right from The Start’.
MATERIAL – Standardization and Quality Consumables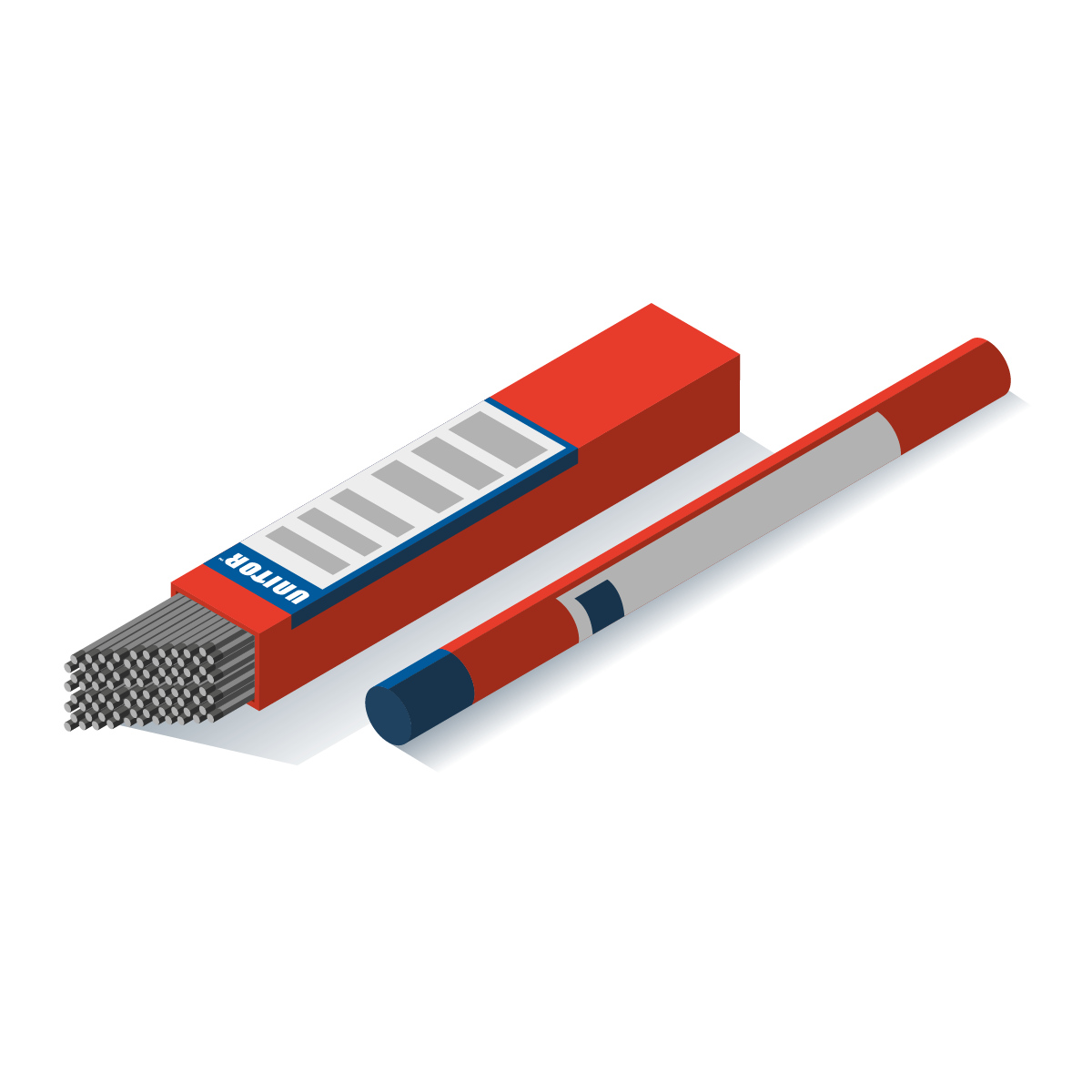
- Using high-quality, standardized welding consumables reduce defects, improve consistency and enhance safety.
- Poor-quality consumables can create inconsistent welds, more fumes and increased risk of poor weldment quality.
- Standardized materials reduce Total Cost of Ownership (TCO) by reducing rework and material wastage.
METHOD – Practical and Proven Processes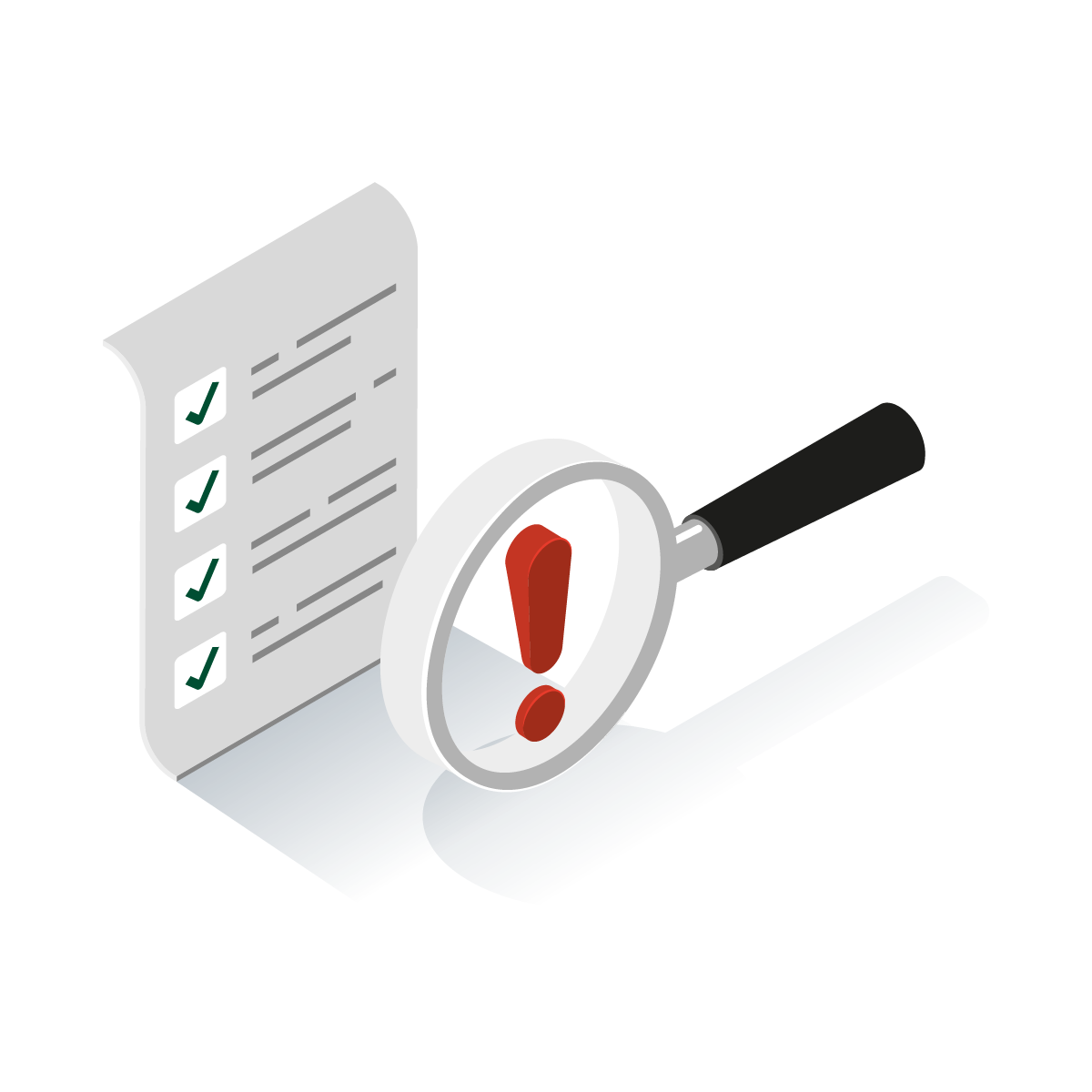
- Procedures shouldn’t be bureaucratic exercises; they must be workable, clear and adapted to real-life scenarios. Shipboard hot work safety should always be aligned with COSWP Chapter 24, emphasizing the best practices and guidelines from equipment selection to permit to work system (PTW) and risk assessments.
- AimZero recommends regular equipment inspections in order to uncover deficiencies such as missing flashback arrestors, damaged cables or hoses and non-compliant welding machines.
- Contractors (who, according to Gard, are responsible for nearly 40% of hot work related fires) must follow the same safety standards with no exceptions.
MEASUREMENT – Monitoring and Learning
- Safety performance must be tracked, reviewed, benchmarked and improved continuously.
- Aim Zero advocates for near-miss reporting, safety audits and knowledge sharing to close feedback loops, turning lessons learned into prevention.
- Linking these safety metrics to ESG reporting gives shipowners a competitive edge with charterers and insurers.
THE REAL COST OF NEGLECTING SAFETY
Some operators still see safety as a cost rather than an investment. This is a dangerous mindset. The real cost of poor hot work safety includes:
Injuries and fatalities |
Equipment or vessel damage |
Operational downtime |
Environmental harm |
Reputational damage |
Skyrocketing insurance premiums |
Figure 3: Welding personal protective equipment must always be used onboard
THE REAL-WORLD EVIDENCE
Former Alcoa CEO Paul O’Neill prioritised Safety Culture when he took over the top job in 1987. The emphasis was on ‘Zero Accidents’ and, despite some hesitancy on the part of his peers and company stakeholders, O’Neill quickly showed that a focus on the most basic needs of the company’s personnel had exponential benefits in other areas of the business.
After just one year, Alcoa’s profits hit a record high. O’Neill had managed to lower the company’s workplace injury rate to one-twentieth of the US average while simultaneously raising annual net income by a factor of five. He asserted that the same habits that ensured reduced workplace accidents paved the way for profitable innovations within Alcoa.
Similarly, if you want to connect your crews with safe behaviours to reduce accidents, increase productivity, improve morale and boost profit, it’s time to invest in proactive and sustainable safety culture solutions.
BUILDING A SAFETY CULTURE: IT STARTS AT THE TOP
Safety culture cannot thrive without visible leadership commitment. AimZero encourages:
- Senior management to champion safety as a core value, not a compliance burden.
- Linking hot work safety to corporate ESG goals. Hot work safety ties directly to the 'Social' pillar of ESG — protecting seafarer welfare.
- Recognizing that safe operations enhance commercial reputation, attracting charterers, insurers and regulators. Charterers increasingly demand evidence of strong safety cultures before signing contracts, while insurers reward proactive safety programs with preferential premiums.
Overall, transparent safety performance feeds directly into sustainability reporting, which enhances your corporate reputation.
WILHELMSEN’S COMMITMENT: SAFETY AS A SERVICE
“As a supplier, it is part of our responsibility to take concrete steps towards improving safety at sea. Aim Zero is part of such initiatives,” says Chris Teoh, Senior Product Manager, Welding & Repair, at WSS.
Through Unitor™ equipment, consumables, inspections, training and technical advice, WSS empowers shipowners to make zero harm a practical reality, not just an aspirational slogan. Conducting a thorough inspection of your welding equipment and environment is the first step to identifying potential risks with your equipment onboard your vessels. Our globally available Welding Safety Inspection service makes it easy for you to elevate your safety onboard
A CALL TO ACTION
Hot work safety is everyone’s responsibility: from shipyard to shore office to seafarer. Fires and fatalities don’t just happen in poor weather or old ships. They happen when we let safety drift into the background.
With AimZero, WSS invites the industry to rethink safety; not as a regulatory box to tick, but as a core part of operational excellence and corporate responsibility. Together, we can embed safety into our industry’s DNA, protecting lives, assets and our shared future at sea.