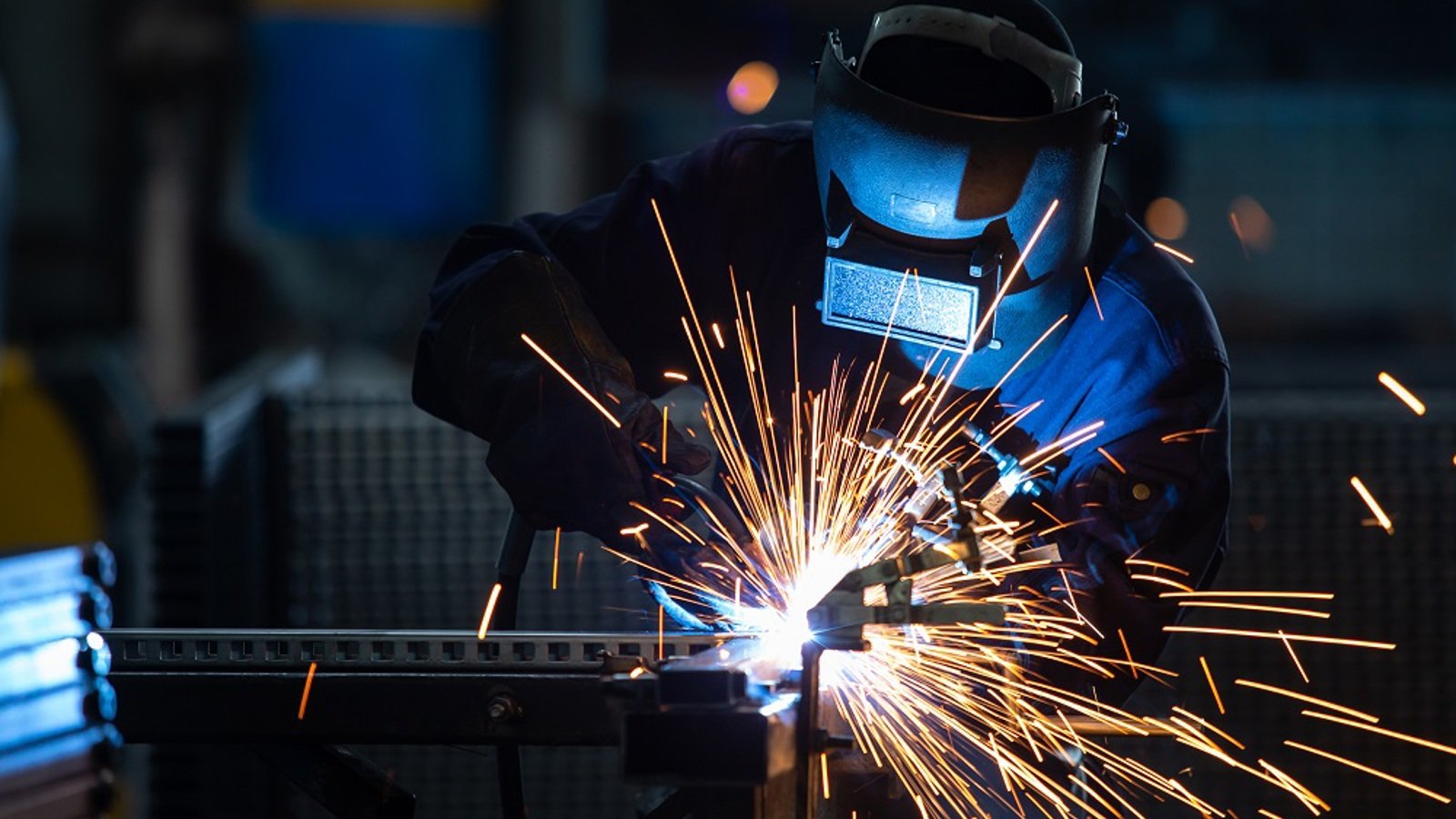
Choosing the right shielding gas for your welding needs on board
Shielding Gas: An often overlooked welding consumable
Arc welding processes commonly used by vessel crew, such as TIG and MIG/MAG welding, require the use of a shielding gas primarily to shield and protect the molten weld pool from the surrounding atmosphere. Elements in the atmosphere (oxygen, nitrogen, water vapour), if allowed to react with the arc and weld pool, will result in problems associated to the quality of the weld such as porosity, cracking and weld spatter. These issues would require corrective action to be undertaken, leading to higher operating costs and time spent.
As it represents a small proportion of overall costs, the right selection of shielding gas available to the crew is often overlooked. However, both crew and vessel owner/manager should understand that the type of shielding gas used can influence penetration profile, arc stability, metal transfer, weld finish and welding speed to varying effect. A sub-optimal pairing of shielding gas to the welding application can be detrimental to weld quality and productivity. It is therefore important to select the right shielding gas for your crew’s welding needs onboard.
Effect of gas mixtures on welding
The type of shielding gas mix chosen depends largely on the welding process and base/filler material. Argon, carbon dioxide (CO2) and their mixtures are typically used as shielding gas for common welding processes and materials on board, both having its pros and cons.
ARGON
Argon being an inert gas does not react with the molten weld pool. This makes it desirable as a shielding gas, displacing the surrounding air and ‘shielding’ the weld pool, especially when welding with non-ferrous metal such as Aluminium. Argon has a lower ionization potential compared to other shielding gases, which improves arc stability thereby eliminating weld spatter and producing a ‘cleaner’ weld finish. On the downside, a lower ionization potential requires lesser voltage input. This limits the penetration depth and becomes less useful for welding thicker material.
CARBON DIOXIDE
Carbon Dioxide is used commonly as a shielding gas due to its relatively low cost and wide availability. Unlike Argon, CO2 is a reactive gas which means as a shielding gas, it has a strong influence on the weld pool. Free oxygen released from CO2 under intense heat of the arc, reacts with other elements to form an oxide layer, called slag, as the weld pool cools. Due to its higher ionization potential, the arc formed is less stable which generates weld spatter. Weld slag and spatter reduces the aesthetics of a weld and may require additional dressing of the weld. When operated at a higher arc voltage, CO2 provides a broad and deep penetration profile to the weld, making it favourable for welding thicker material. Another limitation to consider when using CO2 shielding gas is its inability to produce spray metal transfer mode in the MIG/MAG process which is critical for out-of-position weld control.
ARGON-CO2
Argon-CO2 mixtures with high Argon content combines the benefits of both gases. Compared to pure CO2, a high Argon blend (typically 75% or more) achieves good arc stability, improved quality of weld deposit, and reduced spatter. When compared to pure Argon, the addition of CO2 increases weld penetration and weld pool fluidity. The benefits of such a shielding gas blend result in increased productivity, better out-of-position control and a more visually appealing weld.
Factors to consider in selecting the right shielding gas
Having access to the right shielding gases for your crew’s welding needs on board will result in better weld quality, greater crew productivity, and allows the crew to undertake their maintenance tasks expediently.
Wilhelmsen Ships Service supports your welding needs with 3 types of shielding gases suitable for the most common welding applications on board vessels.
Finally, the type of shielding gas selected depends on various other factors such as the base metal material, metal thickness, type of weld, welding process related to available welding equipment on board and experience of the welder.
For best results, Unitor shielding gases are recommended to be paired with our WSS next-generation multi-purpose welding machine, UNITOR UWW-301 TP, set-up for TIG and wire-welding processes. Click here to learn more.
Trusted welding solutions for maritime use
Due to frequent crew changes on board, it is important to ensure crew with varied skill levels and experience are always equipped with the right tools to carry out maintenance tasks in the most efficient way. Access to the right tools can give the crew extra confidence in performing various welding activities required during vessel voyage and eliminate the need for corrective action and prolonged exposure to welding-related safety risks.
Wilhelmsen Ships Service with its brand ‘Unitor’ has been the market leader in welding technology and products for maritime use for more than 100 years. We provide a total solution for your welding needs on board with a broad range of welding equipment, accessories and consumables.
Benefit from our Global Cylinder Exchange Program and our largest maritime network to have access to shielding gases (and other industrial gases) in ports around the world wherever your vessels go.