Managing fuel quality issues and meeting regulatory requirements
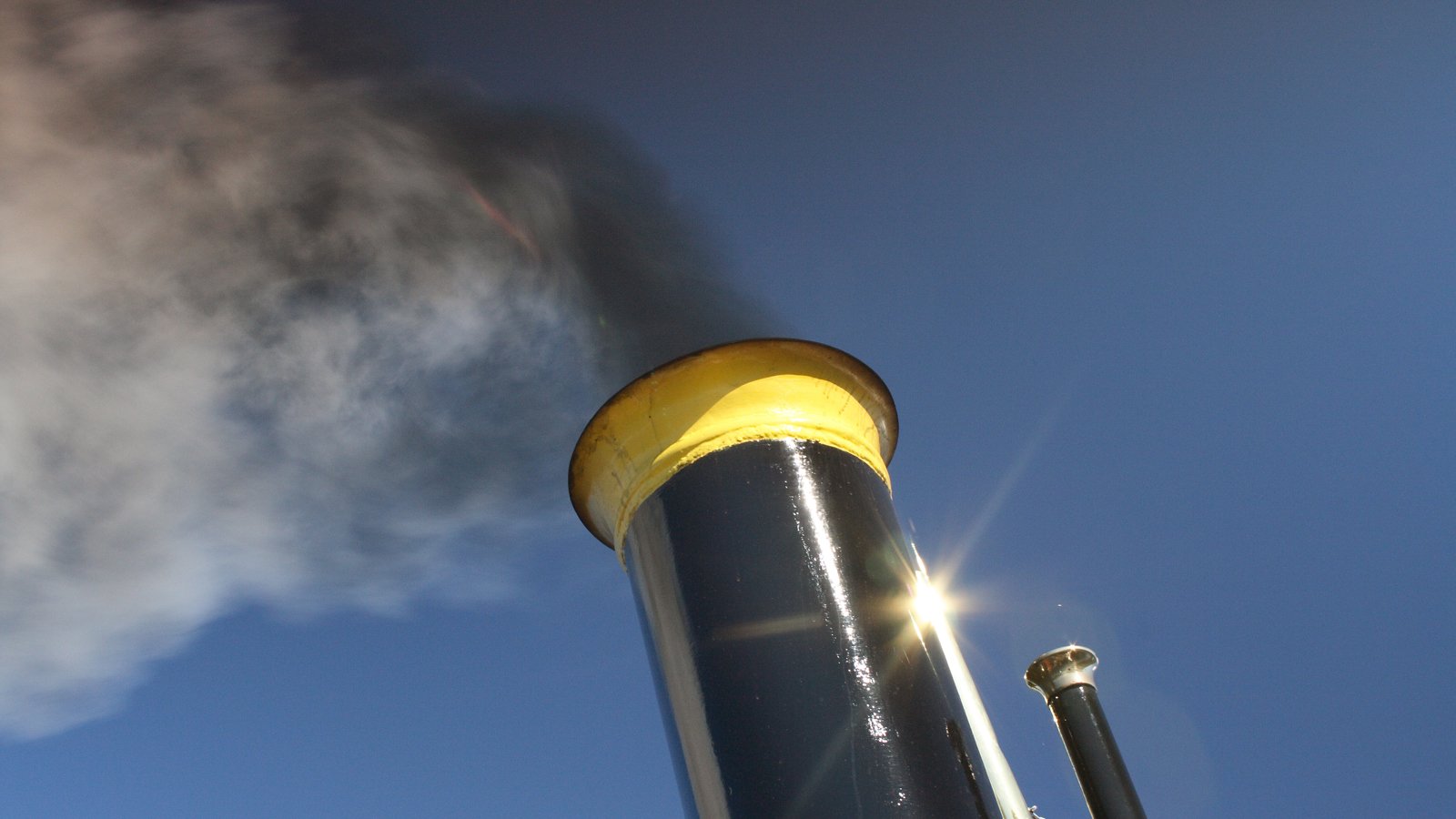
威尔森观察
|
Jonas Östlund, Head of Product Management - Energy Solutions
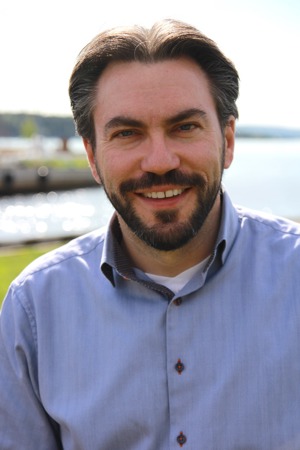
It’s a hard but inescapable fact that the quality of marine fuel used across the world’s shipping fleet has been deteriorating over many years. This has largely come about as a result of changes to the refining process, which have had a serious impact on fuel quality and consistency.
At the same time, environmental legislation designed to reduce sulphur emissions is presenting technical challenges to bunker suppliers and owners, since both low sulphur residual fuels and ultra-low sulphur distillates can exhibit specific problems which can potentially cause problems in operation.
Taken together, these changes will have a profound impact over the next 10 to 15 years as refinery output shifts towards new fuels and the next wave of pollution regulations begins to bite.
Slow steaming into trouble?
Across the maritime industry, the pressure to increase efficiency, reduce operating costs and limit environmental impact is bringing vessel speeds down. The effect of increased costs for the low sulphur fuels needed to operate in the ECAs is being felt at the same time as freight rates remain low for many operators, forcing the requirement to adopt slow steaming procedures.
It is now widely understood that slow steaming can reduce the amount of fuel consumed during a voyage and at the same time reduce carbon emissions significantly. A speed reduction of 20% can lead to more than 30% cost saving on the fuel used and bring a similar reduction in the amount of CO2 emitted.
Yet against these positives, the primary disadvantage associated with slow steaming is that ships’ engines were not necessarily designed to operate under these conditions for long periods. The result can be poor combustion in the engine at low loads, which can reduce efficiency through a build-up of soot deposits in the engine and exhaust gas economiser.
Such problems are exacerbated by the overall decline in fuel quality. When shipping companies buy fuel from bunker suppliers, the product they receive is generally a blend of residual fuels and various cutter stocks. The suppliers must meet the owner’s specification and ISO standards for bunker fuel, and as long as the product meets the agreed specifications, their contractual obligation has been met. These specifications, however, are not a good guide to the real quality of the fuel when presented to the engine or boiler for combustion.
An unstable blend
Because low sulphur residual fuels are today mostly blended to specification from a residual source that has gone through a secondary conversion in a refinery, the fuel’s stability is in many cases very poor.
A particular problem is the increased severity of the viscosity-breaking process used by petroleum refiners to meet the increasing demand for automotive and aviation fuels. The blending process can cause severe instability problems in the fuel which may not be apparent immediately, but which can cause severe problems with asphaltenic sludge in tanks, filters and from the purifier.
The accepted, mechanical means of treating fuels onboard ship are by settling, separation and filtration, all of which have a limited physical effect on fuel combustibility. Fuel problems that begin in the refining process can be aggravated during shipping and blending.
For owners who want to protect their investments, many of these issues can be solved by chemical treatment, which has proven to be an economic solution to improving the quality of the fuel and improve its properties to a reliable level.
Fuel treatment chemicals can be divided into three categories, pre-combustion, combustion and post-combustion additives. The types of additives available today are sometimes combinations of these categories, designed to solve the different problems end users are experiencing.
New fuels, new challenges
The issues discussed above relating to residual fuel will continue to apply on a global basis, even after the global sulphur limit drops to 0.5% in either 2020 or 2025. However, inside the ECAs, where the sulphur content of the fuel used can be no more than 0.1% after 1 January 2015, a more radical change will take place. Owners face the choice of complying with the ECA rules through the use of distillate fuels or alternative abatement methods such as sulphur scrubbers.
Quality problems when using distillate fuels are fundamentally different from those of residual fuels and focus around lubricity, storage stability and microbial contamination. Lubricity problems are most likely to happen in the fuels with a lower sulphur content than 0.1%.
The reduction of sulphur is often blamed for the problems of lubricity with modern fuels. But this is not entirely true as the same refining process during which sulphur is removed also removes other natural lubrication components. This means that fuels with similar sulphur levels can have different lubrication properties, and sulphur level is not always a safe indicator for lubricity properties of a fuel.
Most distillate fuels are vulnerable to degradation through a range of reactions. The results of this degradation can include colour change as well as gum and sediment formation. These can have a severe effect on quality during long term storage and can also induce corrosion of the fuel system.
What is not widely known is that distillate fuel is treated by the refinery with a stabiliser to protect it against deterioration for six months. When these six months are elapsed, the fuel is more or less unprotected from further deterioration. Owners should consider carefully the addition of a multi-function fuel stabiliser during bunkering which will add protection against oxidation, sedimentation, colour change and corrosion.
Practical solutions to fuel quality issues
Understanding marine fuels at a time when their regulation and performance are subject to so much change is an additional challenge to shipowners already facing higher costs and pressure to slow steam in order to maximise earnings. Given the variable quality of residual fuels today and the lubricity and storage issues around low sulphur distillate fuels, there is a clear need for regular testing and treatment to ensure that maximum value can be extracted from the fuel. Testing is the first step in beginning a treatment process when problems are suspected and it is important that potential problems are detected early and steps taken to avoid the time and cost of later remedial action.
And it is critical to understand that many of the problems encountered onboard ship are not related to operation of the engines, but to the fuels used. This clearly underlines the need for fuel treatment to be integrated into the vessel’s maintenance schedules.
Building on 30 years’ of experience delivering fuel treatments to the maritime industry, Wilhelmsen Ships Service’s Unitor FuelPower range applies the most advanced technologies to make certain today’s fuels can be used with confidence, regardless of fuel stability or slow steaming.
The range for use with residual fuels includes FuelPower Demulsifier, an updated demulsifier designed to cope with high water levels in oil emulsions, FuelPower Conditioner, a new treatment for unstable and incompatible fuels which improves fuel reliability and FuelPower SlowSteam, a low dosage combustion enhancer and stabilizer.
To help manage the unique challenges of distillates effectively, Wilhelmsen Ships Service has developed a new product range, Unitor DieselPower, specifically for this fuel type. A series of advanced formulations helps to keep fuels bright, stable and trouble-free, with fewer problems resulting in lower costs in operation.