What lies behind the usability and longevity of a rope?
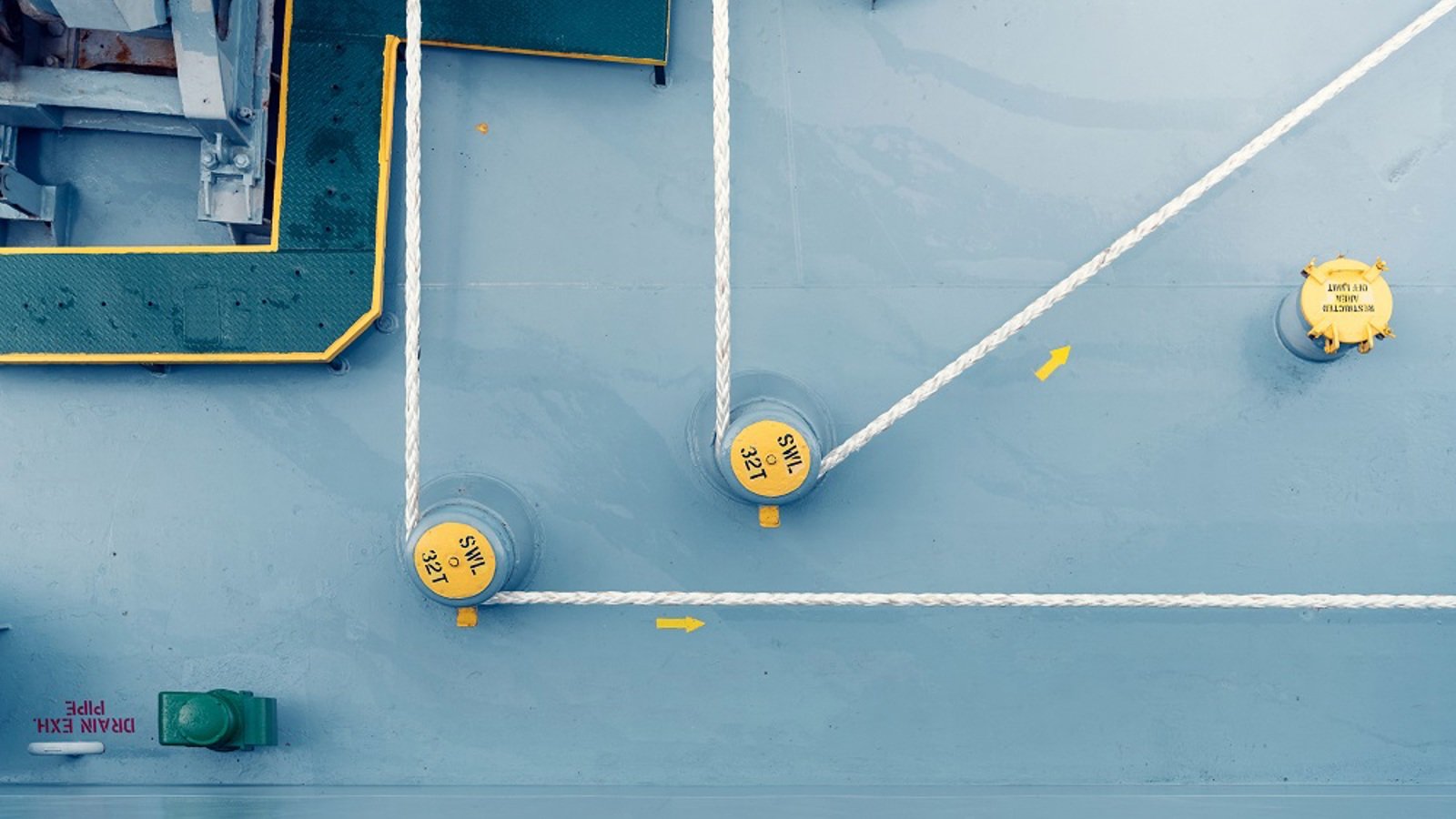
威尔森观察
|
Thomas Caradec, Technical Product Manager, Ropes
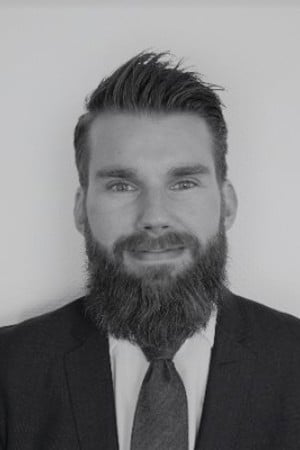
Shipowners are increasingly looking to mooring ropes made from high modulus polyethylene (HMPE) which offer the best strength to weight ratio in the market. At equivalent strength, a HMPE rope is 7 times lighter than a steel wire rope and 3 times lighter than a polyester rope, which increases its usability while reducing the total time spent by crew members on mooring operations and fuel consumption.
Due to their high performance, HMPE ropes are also more costly than most other fibre ropes and their price can vary significantly between rope manufacturers. However, the differences in price, performance, weight and expected lifetime should be considered, not only when calculating operational costs, but also for evaluating the global impact of rope production on the environment.
Rope performance indicators
When it comes to selecting a HMPE mooring rope, there are several key factors that shipowners should consider: abrasion, resistance, diameter, linear density, and strength to weight ratio.
To get a gauge of how the different rope products in the market fare in each of these factors, Wilhelmsen has compared the performance of our Acera ropes against 6 other ropes through extensive laboratory testing.
Rope abrasion
Rope abrasion is one of the most common issues that affect a rope’s longevity. The ability of a rope to resist abrasive damage from rubbing against mooring equipment is critical to prolonging its usability. Rope abrasion also leads to the release of particles into the ocean, which is harmful to marine life. A rope with better abrasion resistance will release less material into the ocean over time, and thus have a reduced environmental impact.
By using quality ropes with high abrasion resistance, you will not need to replace them as often. This allows you to avoid the complexities that come with recyclingand responsible disposal, and causes less waste and damage to the environment.
Currently, there is no standardised method for quantifying the abrasion resistance of a rope. Thus, Wilhelmsen has developed a test bench solely dedicated to testing the abrasion resistance of ropes. Under a constant rope tension, the rope is dragged back and forth on an abrasive surface designed to replicate the steel surfaces in real mooring environments onboard vessels. The process is continued until the rope breaks, and the number of cycles is recorded for each rope.
The following is a table of results of the 7 ropes that were tested.
Compared to other ropes, the Acera rope lasted the longest under abrasion.
Abrasion can be identified by the visible fraying on the rope, which will ultimately lead to the breakage of the rope if the abrasion process continues. Figure 1 below shows the state of the tested Acera rope after going through 4482 abrasion cycles. While there are some signs of fraying, the rope is still largely intact. All the other ropes in this study had broken at this point.
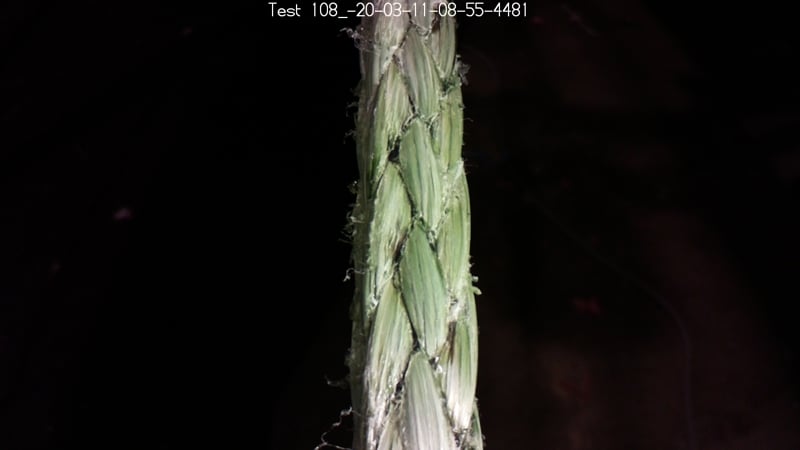
Figure 1
Linear density
Linear density is the measure of the weight of the rope per unit of length (g/m). Ropes with a lower linear density are ideal as they are easier for crew members to handle on deck and require less material to manufacture.
The following is a table of the measured diameters of the 7 ropes and their measured linear density.
Although all 7 ropes are specified to have a nominal diameter of 24mm, most ropes have shown a much larger diameter when measured at the reference tension.
While some variation from the nominal diameter is to be expected, shipowners should note that a large variation from the nominal diameter is likely indicative of a higher amount of material used to achieve the desired rope strength. This results in a larger diameter, and consequently a higher linear density.
Strength to weight ratio
The breaking load of a rope is the maximum force under tension the rope can withstand until it breaks. The higher the breaking load, the greater the force the rope can withstand.
The following table shows the difference between our measurements and the Breaking Load (BL) specified by various rope manufacturers. In addition, the strength to weight ratio of each rope has been calculated using the measured breaking load and linear density.
At equivalent strength, ropes with a lower linear density require less materials to produce, which means less materials going to waste. It is also lighter in weight and easier for the crew to handle.
What are the practical implications of these results?
Abrasion resistance and the amount of material used in the manufacturing of each rope affect long-term costs and environmental impact. It is thus important for shipowners to consider how each rope performs against market benchmarks, before making a purchase decision. In this section, we evaluate and project the cost and material savings of a rope over a 10 and 25-year period.
Assumptions and simplified scenarios
Due to the wide range of factors present in real-life mooring environments on board vessels, it is extremely difficult to replicate the exact scenarios in which test results can be correlated with real-life operations.
Therefore, a simplified scenario was used as the basis for all ropes in these tests, which offered a common basis for comparison. This approach used the expected lifetime of Acera ropes as a basis, which is 8 years in regular operating conditions. The lifetime of the other ropes tested was estimated by indexing the Acera rope’s lifetime with the results from the abrasion test. For instance, if a rope lasted 20% shorter than the Acera rope in the abrasion test, its lifetime was estimated to be 20% shorter.
To cover a wider range of real-life environments, two scenarios were used: one for regular conditions, and one for harsh conditions. The lifespan of Acera ropes in normal conditions is an estimated 8 years, and under harsh conditions, is reduced to 5 years.
The following figure shows the estimated lifespan of the 7 ropes based on the simplified approach described above.
Impact on cost
Initial purchasing cost
The following figure shows the cost of ropes in this study compared to Acera Amundsen rope.
There is a large variation in unit cost of the ropes, with the most expensive rope being 2.3 times more expensive than the cheapest alternative. The list price of Acera ropes is below the average unit cost of ropes in this study.
However, in order to evaluate the total cost of ownership of the ropes, it is more relevant to look at the total cost of ropes over a longer period of time.
Cost over 10 and 25 years of operation
Based on the lifespan of the different ropes shown in Figure 2, it is possible to calculate the number of ropes that will be used over a period of 10 and 25 years. These calculations are for a set of 16 mooring lines, which amount to typically a full set for large vessels. This allows us to calculate the total cost for ropes over those periods, as shown in the figures below.
Thanks to their longer lifespan, Acera ropes offer the lowest cost of ownership over a 10- or 25-years period. Over 25 years, Acera ropes can offer a cost saving of over 1 000 000 €.
Taking steps to reduce our environmental impact
Wilhelmsen takes our impact on the environment very seriously, and is constantly taking steps to design high-quality, long lasting products to reduce waste and environmental damage.
Using a similar approach to the cost calculation, the total amount of material used for producing the ropes in this study can be calculated. The calculations use the number of ropes that will be used over a period of 10 or 25 years, multiplied by the total weight of each rope.
During mooring operations, the ropes will be subjected to abrasion, which will cause plastic particles to be released into the environment. Ropes with better abrasion resistance will release less materials into the environment over time.
Additionally, due to their longer lifespan and lower weight, Acera ropes require a lower amount of HMPE material in manufacturing over 10 and 25 years. This also reduces the amount of material released into the environment at the end of life of the product.
About Timm's Acera ropes
Compared to equivalent HMPE ropes from other manufacturers, Timm's Acera
ropes offer superior performance in abrasion, diameter, weight, and strength to weight ratio. When translating those results into real life application, this study has demonstrated that Acera ropes can offer significant cost savings over long periods. In addition, thanks to their best-in-class abrasion resistance and strength to weight ratio, Acera ropes will have a lower impact on the environment compared to other HMPE ropes on the market.
For more information on our range of Acera mooring ropes, visit this page.