Why improper mooring tail selection compromises safety
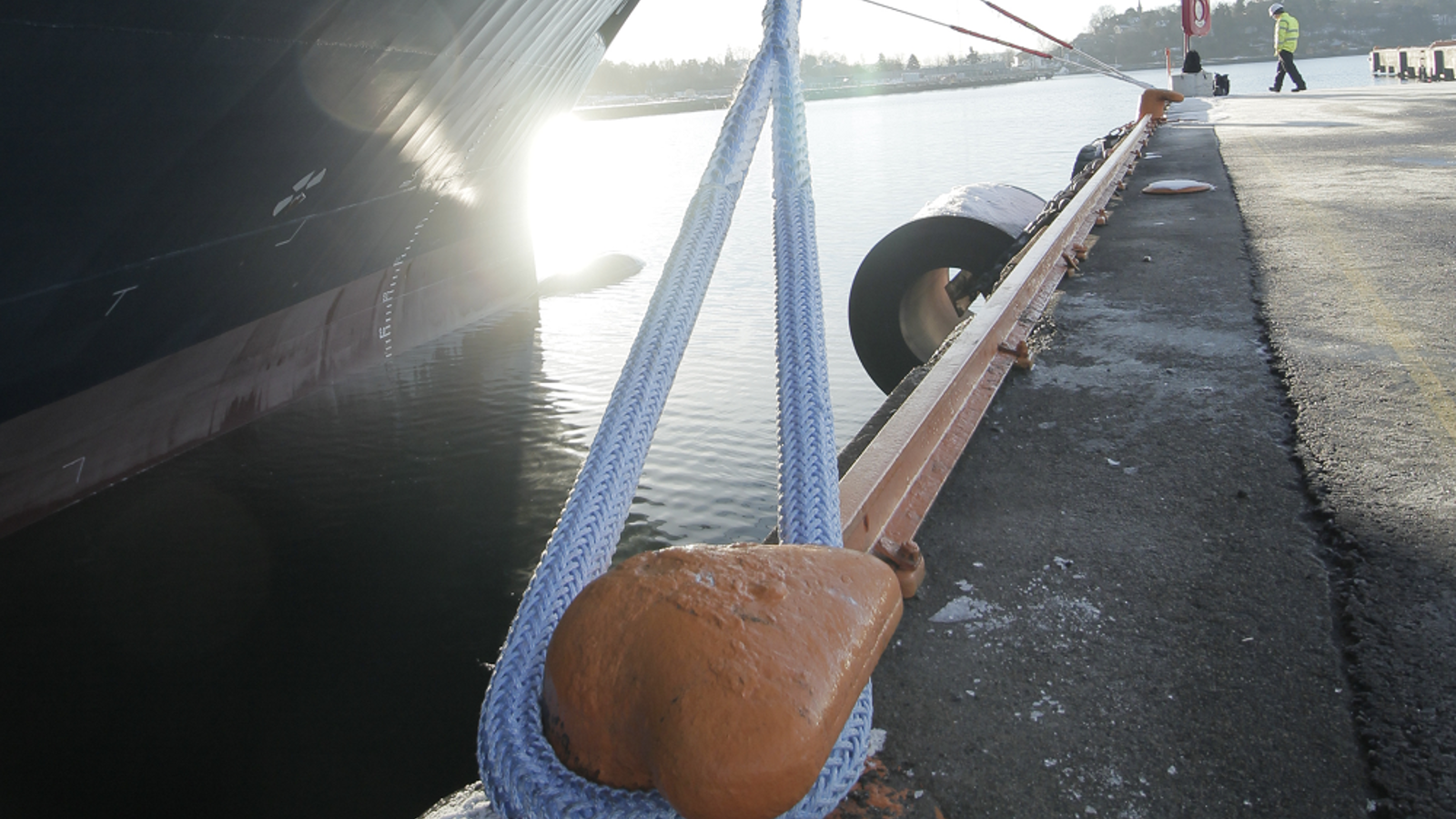
威尔森观察
|
Thomas Caradec, Technical Product Manager, Ropes
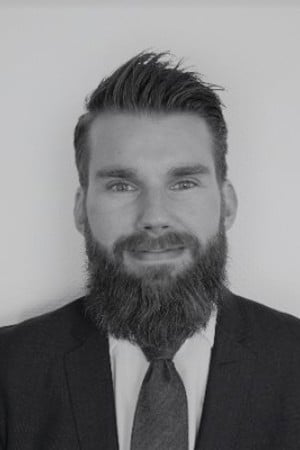
The OCIMF Mooring Equipment Guidelines 4th edition (MEG4) describes industry best practice for mooring rope operations and design. The guidelines recommend that tails should have approximately 25% higher strength than the rope used in the same mooring line. The regulations are primarily focused on LNG and oil/chemical tankers, so it is not the case that all vessel types should follow them.
Getting things straight
“Customers buying HMPE ropes usually buy tails at the same time. However, some that are not bound by MEG4 will sometimes use tails with lower strength than the rope, because they want to be sure that the tail is the element that will break first in the rope-plus-tail assembly. Ropes are much more expensive to replace than tails, and it is much easier to replace a tail than the main line. This represents a challenge that needs addressing,” says New York-based Levis, one of Wilhelmsen’s rope experts.
“I’ve also been asked by some vessel captains to provide tails of a weaker strength than the main line, so the tail will act as this ‘weak link’. They confirm it’s easier to replace the tail than the main line. While that is true when a tail breaks, in a properly managed mooring arrangement neither the main line nor the tail should break, and they should be retired before there is a risk of them breaking unpredictably,” he says, emphasizing that if a line or tail breaking is a consistent occurrence, then the mooring arrangement and line management should be re-evaluated.
“Customers should also be aware that when you buy a rope and tail with the same working strength, in reality the tail wears much faster. That’s why, in the market, tails get replaced a lot more frequently than ropes. A weaker tail will soon get even weaker and may become a safety concern. In addition, the rope is likely to see increased load when paired with a weaker tail, which means the lifetime of the rope will be reduced. This should dispel the myth of buying a weaker tail in order to conserve the rope.”
“Tails are recommended to be 25% to 30% stronger because that percentage is eaten up quite fast. However, some find it difficult to grasp that buying something 25% stronger is actually weaker.
Choosing to buy a lower-strength, lighter mooring tail than the rope is a misguided strategy that can compromise the integrity of your entire mooring configuration and the safety of those tasked with handling the lines.
Why do tails degrade faster?
“The reason for tails losing strength is that when they are in operation – whenever the vessel is moored at the quayside – they are continuously subjected to various damage mechanisms that can potentially lead to material failure. The three primary mechanisms are dynamic load, fatigue, and abrasion. Tails are connected to bollards, as well as sometimes sitting and working from the fairleads. In other words, they really work hard and suffer a lot more than the rope,” says Levis.
Dynamic load is a constant process of high load that comes on the line quickly and rapidly disappears again. These sudden load fluctuations are called shocks, and the effect is greater on short lines than long ones. One effect is that the typical properties of the tail (and rope) can change over time.
Fatigue is the process of alternate tension-tension and/or tension-compression cycles that can also eventually lead to failure even with low or moderate loads. Cyclic loading subjects the tails to an increasing rate of fatigue resulting in reduced strength over time.
Tails typically have a higher elongation than the main line and are designed to absorb those dynamic and cyclic loads in order to preserve the main line, which is why the tails work harder and wear faster than the ropes.
Abrasion is surface wear due to contact with other fibres or contact surfaces i.e., bollards. Tails are also frequently dragged along the ground by the port workers, sustaining material damage.
Tests conducted on used ropes and tails in our R&D department have revealed that tails can undergo a substantial reduction in breaking strength in a relatively short period of time compared to main lines. Hence the industry term ‘weak link’*. “How long it takes for tail strength to degrade below the strength of the mainline will depend on mooring conditions and handling,” says Levis.
*Note that in typical mooring arrangements the actual weakest link is the winch brake rendering, which is set to release at 60% of the Ship Design MBL (Minimum Breaking Load).
Heeding the guidelines pays off
Using the recommended 25% to 30% extra strength on the tails will ensure they are able to endure the mechanical damages and loads described above. “Due to the rapid decrease in strength, the tails will be the weak link of the assembly for most of their operational lifetime, but they will retain sufficient strength to ensure safety and reduce damage to the main line,” adds Levis.
“Following a prudent safety policy to buy tails with the appropriate strength, as well as careful operational management, will ensure that the integrity of your mooring configurations is not compromised. That should be top priority to maintain safety,” he concludes.
Visit our New era of safer mooring page for more information on our total mooring solutions, including products and service offerings.