Why not all anti snap-back rope solutions are equally engineered
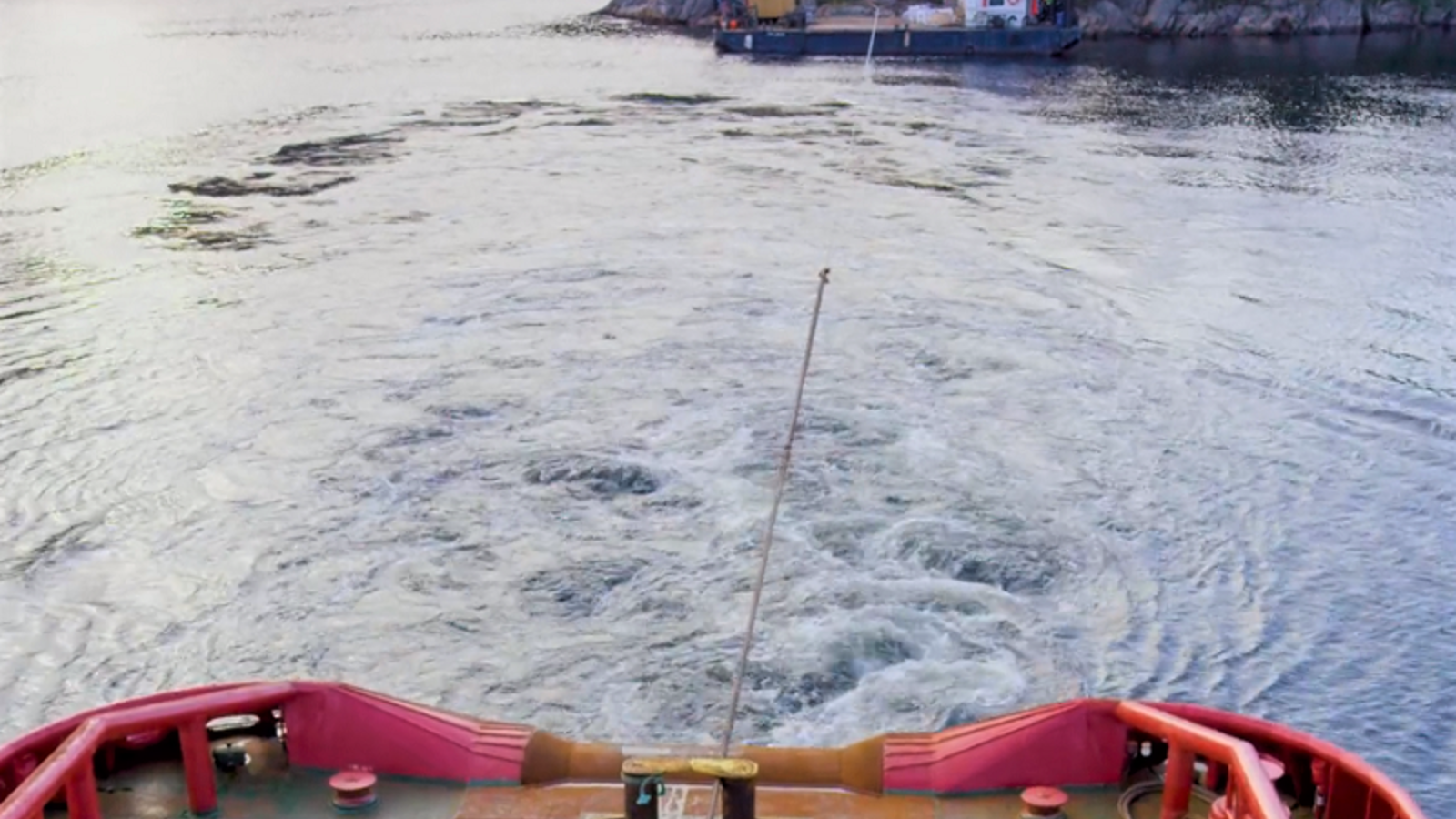
威尔森观察
|
Thomas Caradec, Technical Product Manager, Ropes
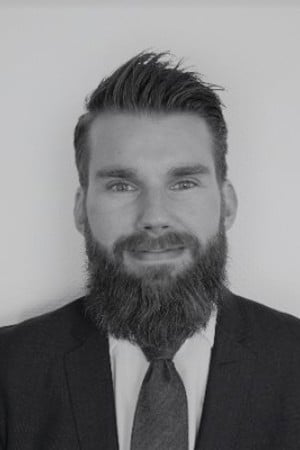
When a mooring line snaps, it can move up to 800km/h. As a result, vessel mooring remains one of the most dangerous tasks crew, and port workers can undertake.
Snap-back accounts for a staggering 53% of mooring accidents, with 1 in 7 accidents resulting in fatalities, according to the UK P&I Club. This cannot and should not continue, and we are glad to see that several anti snap-back rope designs are now offered on the market to address this issue.
However, there is no standard test program to verify the performance of anti snap-back ropes, and it is difficult to verify the claims of improved safety without performing an extensive evaluation.
Unreliable anti snap-back systems perform poorly and create a false sense of security, thus increasing the risk of injury instead of reducing it.
How can you ensure that the anti snap-back rope you have selected will perform as intended when the safety of your crew and the port workers is at risk?
About elongation and snap-back
Elongation is one of the most important characteristics of a rope. The elongation is dependent on the tension applied to the rope and is often express as a percentage of the rope length at rest. A rope’s elongation is governed by its design, construction and the materials used.
Elongation is extremely important for a rope as their capacity to elongate allows them to compensate for the different movements of a vessel during mooring operations resulting from wind, swell and tides among other factors.
When a rope elongates, it behaves like a rubber band, and will store energy in the form of elastic potential energy. The more tension is applied to the rope, the higher is that potential energy. If a heavily loaded rope snaps, that potential energy will be released in the form of heat and kinetic energy, and the broken section would travel on a random trajectory at high velocity. This phenomenon is often referred to as Snap-Back, and the combination of high speed and randomness makes it extremely dangerous.
Why not all anti snap-back designs are equal
Several solutions have been evaluated and discarded throughout our own SBA technology before reaching the optimal and safest design. Unfortunately, several of those “discarded” solutions are now offered on the market as anti-snap-back technology. We will explain why some designs may not provide the expected performance. Here are the findings:
Ropes jacket/cover acting as the anti snap-back element
This initially appeared to be a promising solution in our research. Designing the rope jacket to contain the load-bearing element in case of rope failure may seem to be a good solution to reduce the snap-back effect.
However, the main function of the jacket / cover is to protect the rope from external damage and as such is the first element of the rope to be damaged due to the following elements:
- Mechanical damage (cuts, etc.)
- Abrasion
- UV radiation
- Chemical damage
The rope jacket typically sustains damage and undergoes repairs during the lifetime of a rope. This raises a critical question: how do you ensure a damaged/repaired jacket will still be able to reduce snap-back?
This solution has been tested in our R&D facility with unsatisfactory results. The conclusion from these tests was that the behaviour of the anti snap-back cover is difficult to predict and, as such, is not a safe and reliable solution.
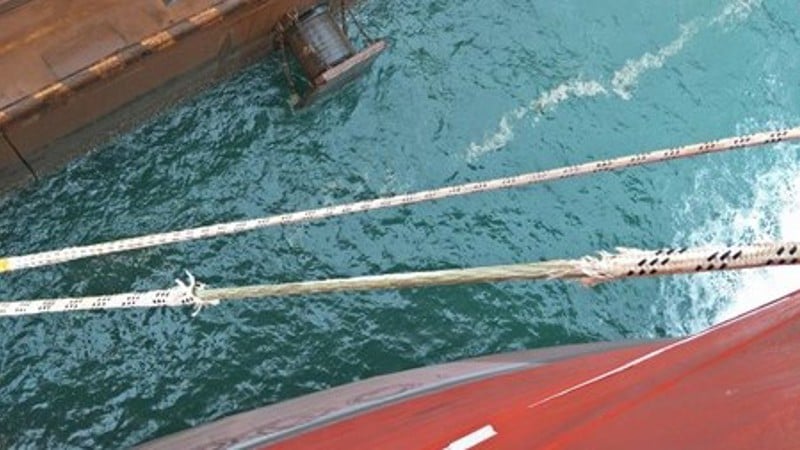
Figure 1: Damaged jacket on a mooring rope
Rope core acting as the anti snap-back element
Rope cores are often used in laid ropes as a supporting element for the rope strands. They are usually made of the same, or similar material as the strands of the rope, which means their elongation is similar.
However, because the core is shorter than the strands, it is the first element of the rope to break under tension. This solution has also been tested in our R&D facility with unsatisfactory results. The conclusion from these tests was that the core of the rope cannot be considered an anti snap-back element.
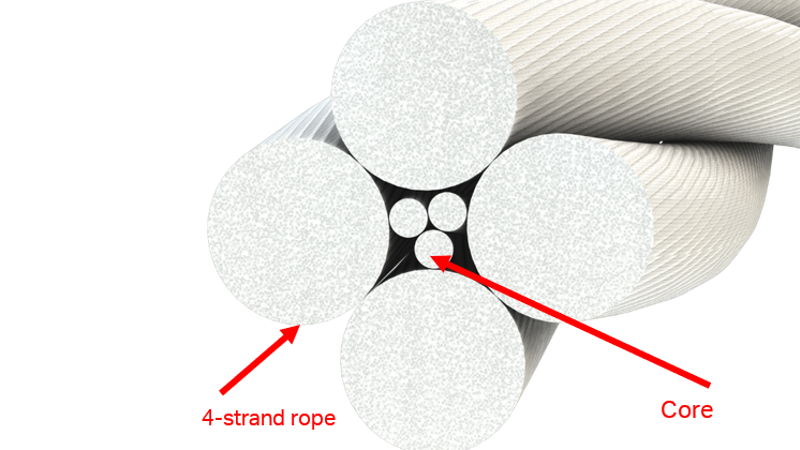
Figure 2: 4-strand rope with core
Using one rope strand as anti snap-back element
Another approach was to consider that one of the rope strands will act as an anti snap-back element. That “anti snap-back strand” would be made of a material with more elongation and thus able to absorb some energy and delay the complete failure of the rope.
However, because of the design of braided ropes, the total length of the strand would not contribute to reducing the snap-back effect due to pressure created at the braiding points between strands when the rope is tensioned.
These pressure points cause the ‘anti snap-back strand’ to be partitioned into small sections each a few centimeters long. Even if using a material with high elongation (e.g. 20%), these small sections are only able to elongate a couple of centimeters and can absorb very little energy in the case of snap-back. This solution has also been extensively tested in our R&D facility with unsatisfactory results.
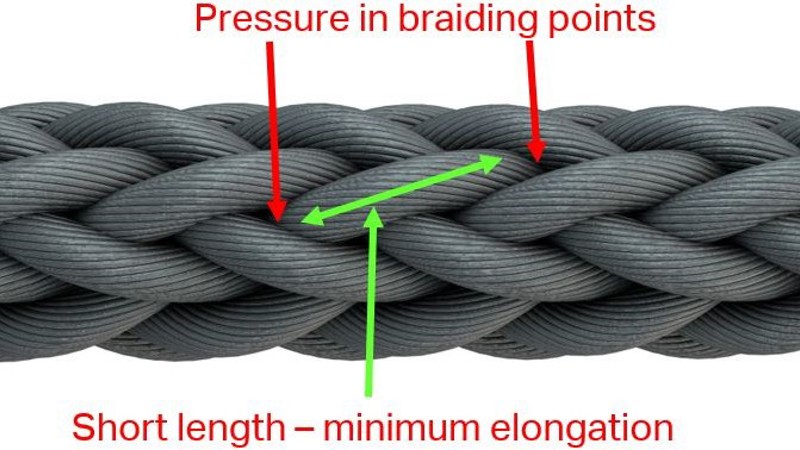
Figure 3: Pressure in braiding points
HMPE ropes do not have snap-back
HMPE ropes are sometimes considered to not have a snap-back effect due to their low elongation. HMPE ropes still elongate under load and the stored energy is still released in case of rope breakage, resulting in snap-back. Claims that HMPE ropes are anti snap-back solution create a false sense of security for the persons operating the ropes and can lead to a dangerous situations.
Lack of recognized standards for anti snap-back technologies
Since anti snap-back ropes are a recent technology, there is currently no standard or guideline to verify the performance of the anti snap-back function. MEG4 guidelines or type approval from class societies typically cover the performance of the rope itself, not of its anti snap-back function. Therefore a type approval or a design certificate on a rope doesn’t guarantee the performance of the anti snap-back function.
How to select the best anti snap-back solution?
When selecting a rope with a purported anti snap-back function, how do you evaluate if the performance claims can be trusted? We recommend verifying the following elements to select the most reliable solution.
Verified and tested by class society
Approvals and verifications from industry leading class societies provide shipowners with an unbiased third-party assessment, and are a great indicator as to whether the product is of the quality promised by the manufacturer.
Class societies such as DNV have developed recommended practices for the qualification of new technologies that include stringent processes and test programs (e.g. DNVGL-RP-A203 Technology qualification). Class societies can provide certificates or verification statements, ensuring compliance with those practices.
Extensive development and testing
The development of a new technology such as an anti snap-back rope requires a dedicated R&D department with dedicated testing equipment. When selecting an anti snap-back rope, shipowners should evaluate the R&D capacities of the rope suppliers and ask for evidence of extensive product testing.
Tested in real-life operation
Although a controlled laboratory testing environment offers a great indicator of product performance, not all factors can be combined in a laboratory setup. Real-life testing introduces additional factors which can sometimes lead to product failure under testing. Therefore, real-life testing of the product in a simulated environment is used as critical verification of a new technology.
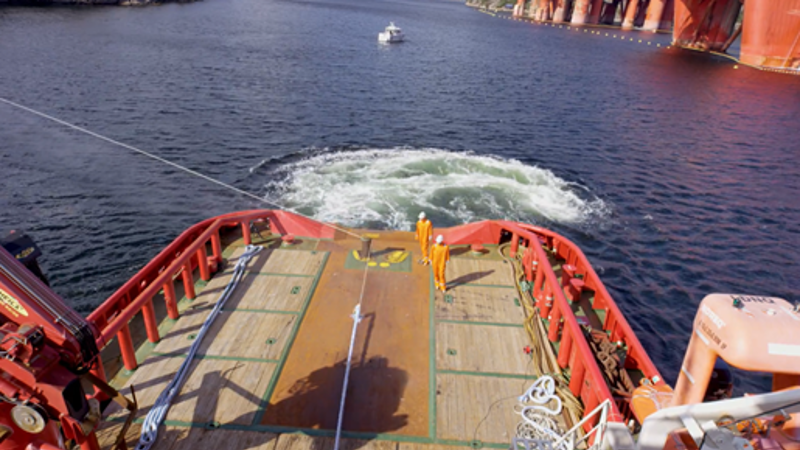
Figure 4: SBA rope broken during real-life testing
A field proven technology
The final proof of performance is a product’s track record in the field. Multiple successful operations of the rope in different dimensions, different environments and by different people, show the robustness of the product and provides confidence in the technology.
Timm Snap Back Arrestor (SBA) design
We have spent considerable resources and close to seven years of development and testing to design a reliable anti snap-back system, called the Timm Snap Back Arrestor (SBA).
Before designing the current SBA solution, our internal R&D department evaluated, tested, and discarded the flawed designs described earlier in this article. As a result, countless trials and errors have been necessary to achieve the optimal and safest design.
The SBA core rope is placed in the centre of the main rope in a way that allows full utilization of its elongation. The method for securing the SBA core to the ends (mooring eyes) has been specially developed for this application. Placing the SBA in the middle of the rope is possible thanks to the hollow construction of 12 strands ropes. Therefore, the SBA feature is only available in our 12 strands ropes and tails.
The SBA is non-load-bearing during normal rope operation. In the event of rope breakage, thanks to its higher elongation, it will absorbs part of the energy released and also ‘guides’ the broken strand(s) along the current axis of the rope, resulting in a significant reduction of snap back.
If load is still applied after the breakage of the rope strands, the SBA will start to bear the load and elongate before breaking itself. However, it is not capable of sustaining high loads and will therefore release much less energy when it breaks.
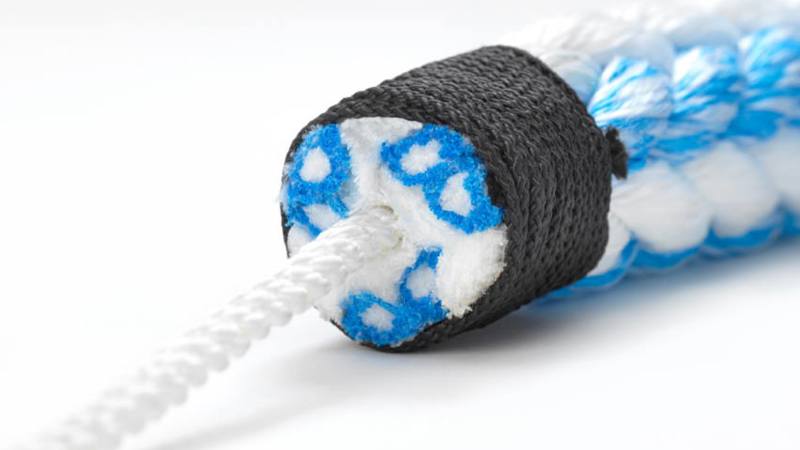
Figure 5: Timm Master 12 SBA
Tested and reliable
Timm SBA has been tested and verified through an extensive testing and qualification program, in accordance with DNVGL-RP-A203 Technology qualification.
The solution has been tested in a real-life operation with an actual tug vessel in Flekkefjord, Norway where the performance of ropes with SBA was compared to ropes without SBA. These tests have demonstrated that the ropes equipped with SBA present a much lower risk to personnel in case of rope breakage.
Watch the SBA mooring ropes live testing video here.
Setting the standard
Since introducing our ropes with SBA solutions in 2019, we have received numerous feedback from customers stating that Timm SBA had significantly reduce the snap-back effect of the broken ropes. Their effectiveness in preventing major accidents has been endorsed by shipowners, crew, port terminal personnel, and other stakeholders as a gamechanger in the maritime industry.
Figure 6: Broken Timm Master SBA rope onboard vessel. The snap-back was reduced thanks to the SBA.
A trademarked name
SBA is a trademarked brand name and only ropes supplied by Timm can bear the SBA™ name. This is to ensure that our customers can trust that all SBA™ branded ropes have been developed and tested according to the thorough process described in this document.
Conclusion
Through extensive R&D and testing, we have developed substantial knowledge about anti snap systems before launching the Snap-back Arrestor technology. Since its introduction to the market, Timm’s SBA has helped reduce the dangerousness of snap-back incidents in real-life operations.
Safety of the crew and port workers is paramount, and there should never be any compromise on safety. We are glad to see more anti snap-back products launched on the market every year, making mooring operations safer globally. However, we believe it is vital for our customers to know that not all anti snap-back systems offer the same level of risk reduction.
Unreliable anti snap-back systems perform poorly and create a false sense of security, thus increasing the risk of injury instead of reducing it. Therefore, it is crucial to evaluate the performance of different designs when selecting an anti snap-back rope.
Extensive testing programs, field-proven products and a technology verified by a leading class society are some elements that can help shipowners select the most reliable and safest anti snap-back solution.
The Snap-back Arrestor (SBA) is available as part of our Timm Master 12 and Acera ranges of rope and our Timm Master 12 tails.
Click here for more information on our total mooring solutions, including products and service offerings.
Browse or download the pdf version here: