Corrosion Prevention in Steam Boiler Systems
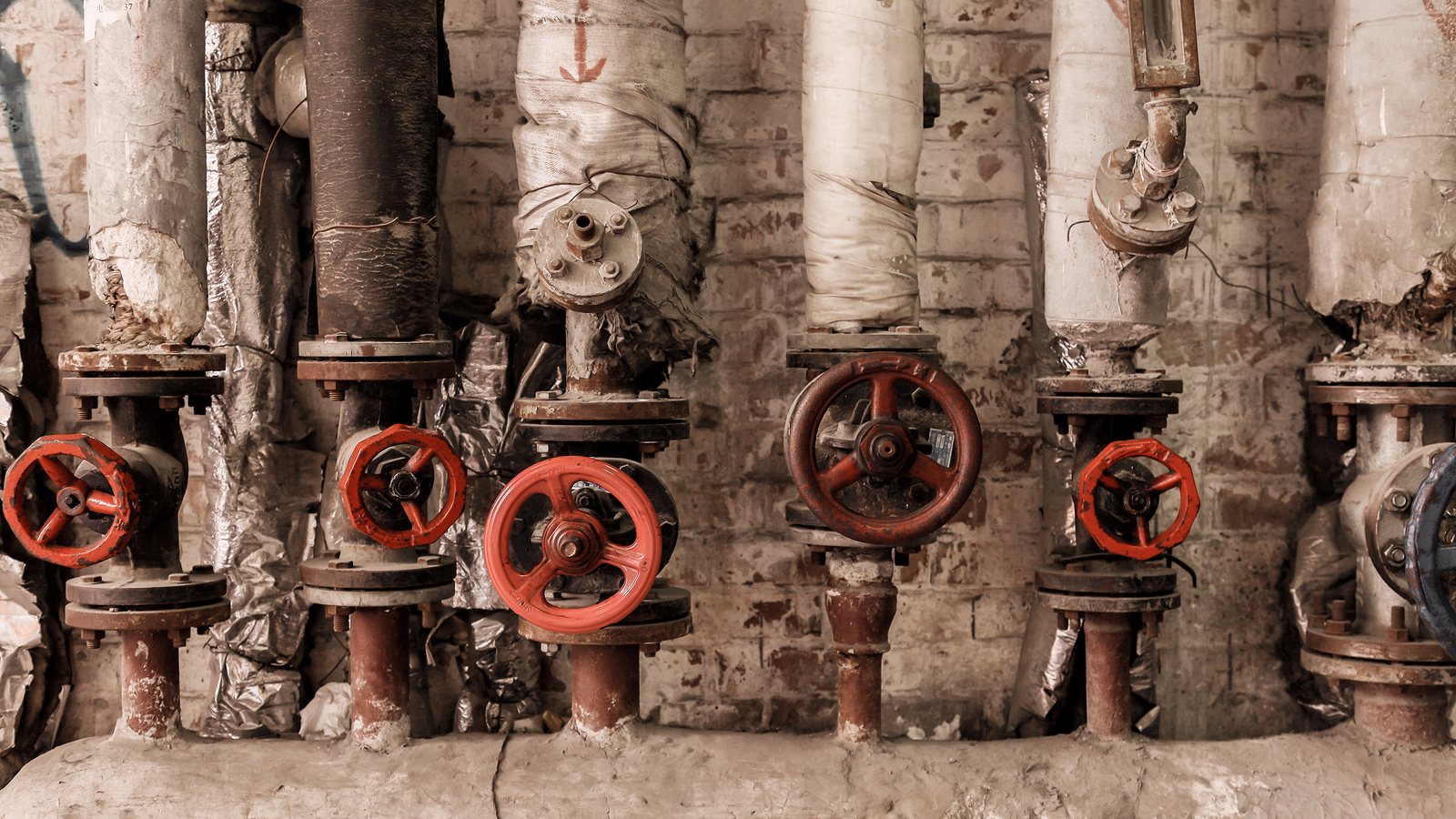
威尔森观察
|
Rune Nygaard , Business Director Technical Water Solutions
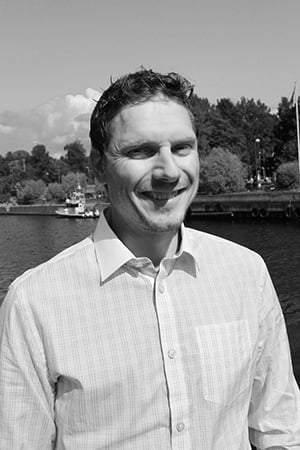
The majority of Marine steam boiler systems operate using high quality supply from on board evaporator systems. This quality of water helps to greatly reduce the problems associated with scale deposition and overheating. The most common failure and repair issue is the damaging effects of corrosion. It is estimated that there are many cases of failure and repairs due to boiler system corrosion notified to Class Society’s each year. The cost of boiler repairs due to corrosion can be in the order of $50,000 to over $1m, plus cost of time off hire. These significant costs often go unrecognized as many are covered by insurance claims. However, in the end, the marine industry will bear the cost, reflected back in higher insurance and deductible costs.
The cost of boiler repairs due to corrosion can be in the order of $50,000 to over $1m, plus cost of time off hire. These significant costs often go unrecognized as many are covered by insurance claims.
Effects of Corrosion
In the steam boiler system, the primary routes for corrosion are due to the presence of oxygen in the feed, boiler and condensate waters and the risk of acidic type corrosion due to reduced pH in the condensate water. These types of corrosion are localised and aggressive and can quickly degrade metal pipework and lead to failure.
Examples of Pitting Corrosion on boiler tube
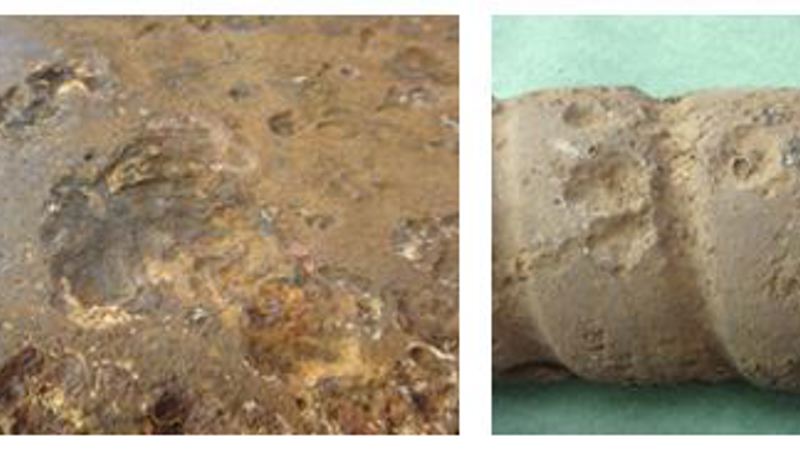
Example of Condensate Line Corrosion
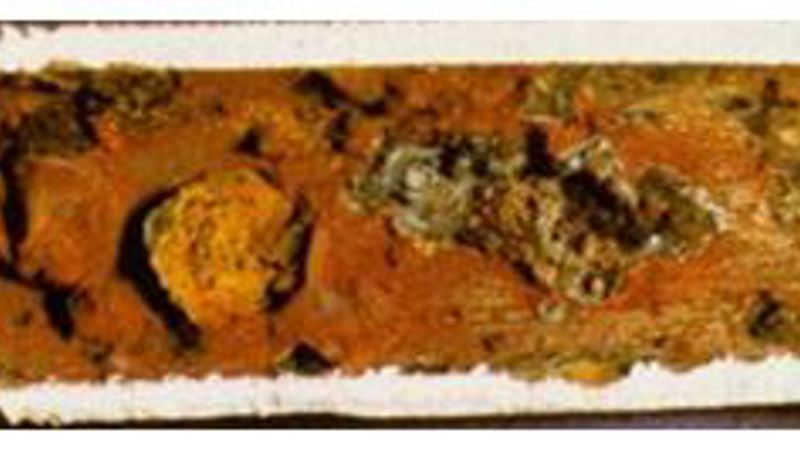
To control the risk of the corrosion we must take a quality approach to the problem:
- Assess the risk
- Select the optimum boiler treatment programme
- Apply the best chemical application approach
- Implement a good monitoring and control scheme
- Ensure that crew are adequately trained
Assessing the risk of corrosion
In considering the risk of corrosion, the primary factor is to have and understanding of the amount of oxygen that is entering the boiler water system. Fig.1 shows that this is related to the temperature of the boiler feedwater. It is important to aim to achieve a boiler feedwater temperature in the range 85 to 95oC to reduce the available dissolved oxygen to around 2.3 to 1ppm. We must take care not to have too high a feedwater temperature as this may give rise to cavitation on the feed pump impellers.
Other methods of physio/mechanical treatment such as de-aeration can also be considered. Such equipment can reduce the dissolved oxygen level to around 0.01ppm. However, space restriction and cost usually limit installation on board ship.
Fig.1 Dissolved Oxygen vs Temperature
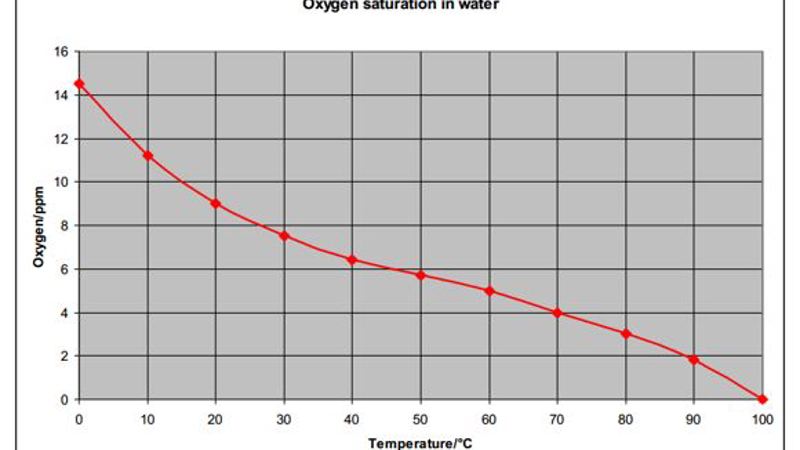
Selecting the boiler treatment programme
The optimum treatment programme should incorporate a chemical oxygen scavenger to remove the remaining oxygen and have the property of forming a passive magnetite layer on internal metal surfaces, which provides enhanced protection against corrosion. A volatile amine treatment should also be selected which carries over with the steam and provides corrosion in the condensate system by raising the pH of the condensate water. Scale and Alkalinity control treatments are also used to maintain clean heat transfer surfaces and help with corrosion protection.
Fig. 2 Example of non-passivated and passivated metal surfaces.
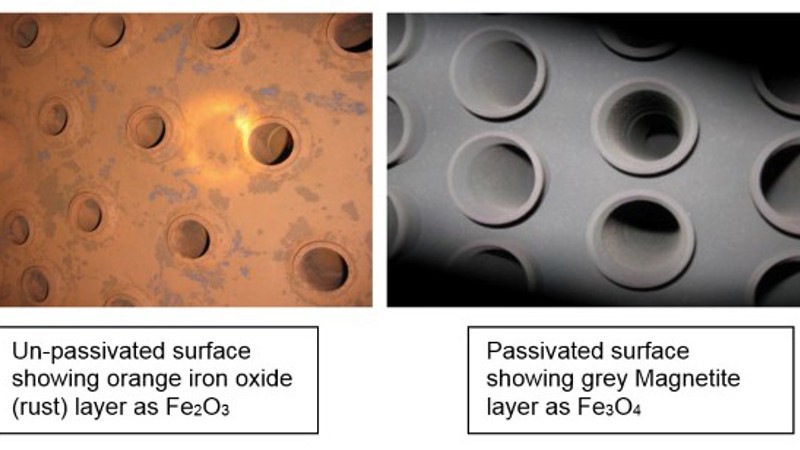
Fig. 3 Properties of Oxygen Scavengers
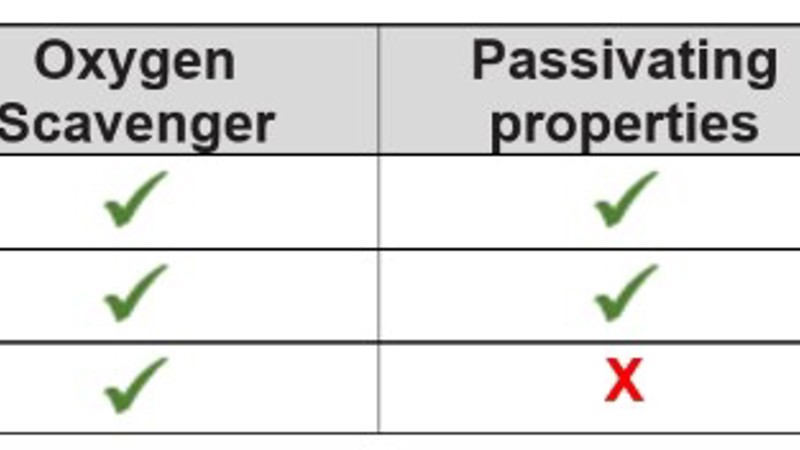
Fig. 3 shows the properties of commonly available Oxygen Scavengers. Hydrazine and DEHA are the most widely used because of the combined Oxygen Scavenging and Passivating properties. Major boiler manufacturers and Class organisations strongly recommend such technologies because of this dual activity.
Chemical Application
Once the boiler treatment programme has been selected we need to consider how best to apply the treatment chemicals to the boiler system. The treatment chemicals should be applied:
- Right time
- Right place
- Right quantity
- Best Health and Safety option
The best option for accurate chemical application and best Health and Safety considerations is to utilise an appropriate chemical dosing system. Automated dosing systems reduce the need for chemical handling and improve the control of chemical addition.
Monitoring and Control
Once the chemical treatment programme is being applied, we must put in place a suitable monitoring and control programme. This takes the form of a range of simple chemical tests that are carried out on water samples from the boiler system. Because we are dealing with a dynamic, high-pressure water system, it recommended that such tests are carried out daily. Results should be logged, monitored, and corrective action on out of specification results taken promptly.
Boiler manufactures advice on activities such as correct blowdown procedures must be followed.
Crew Training
An important factor in the success of the chemical treatment programme is to ensure that crew involved with the application are well trained in the principles of water treatment control and safe chemical handling.
If we take the above approach we will have the best options for asset protection and eliminate the risk of unplanned shutdowns and maintenance and repair costs.