Optimizing Vessel Performance During Lay-Up Management
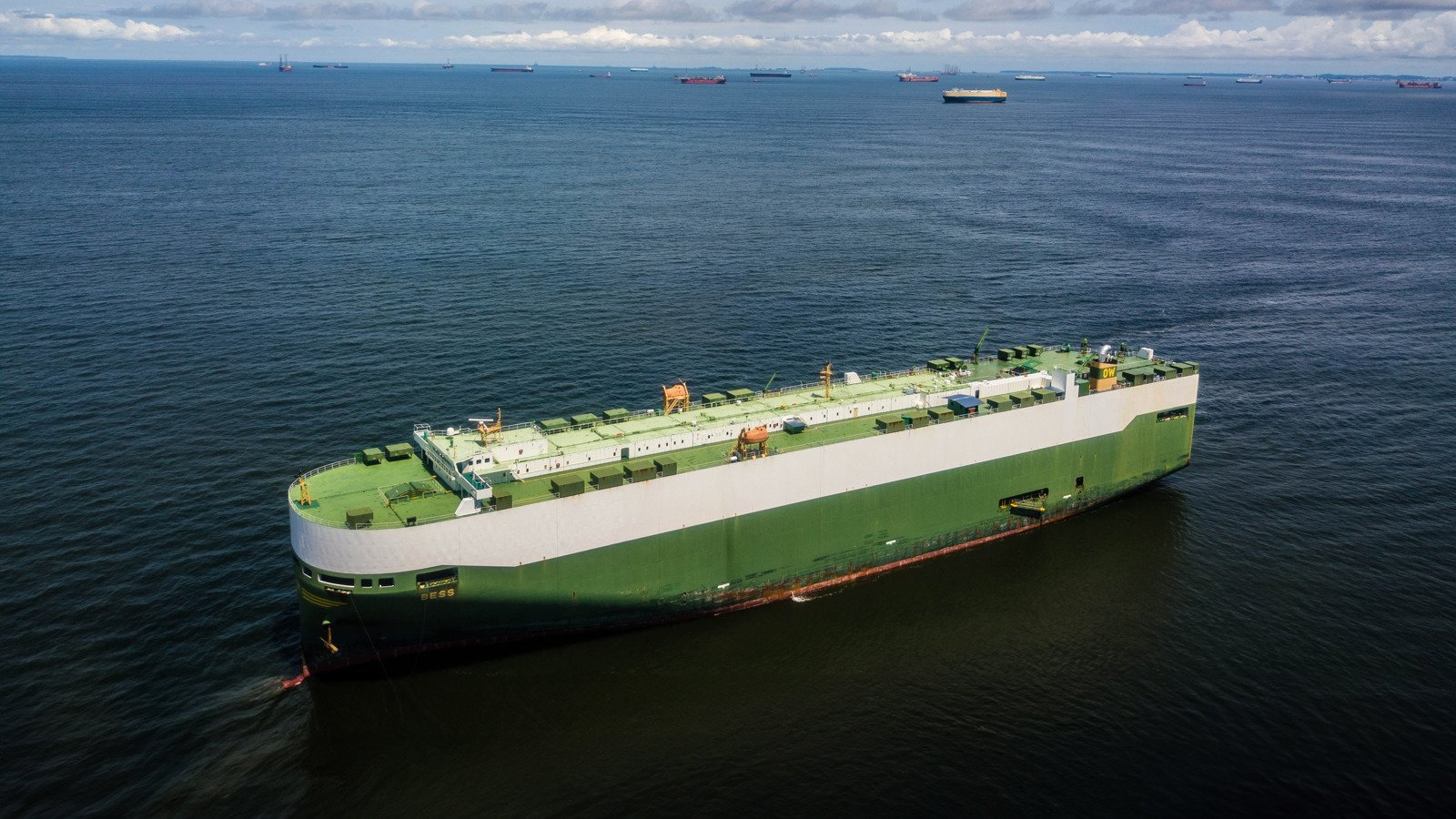
Wilhelmsen insights
|
Wilhelmsen Ship Management
Lay-up is a crucial phase for vessels facing market fluctuations or temporary inactivity. To maximize efficiency during this period, we carefully select optimal lay-up sites, implement rigorous maintenance protocols, and conduct continuous monitoring, including weather, vessel safety, and GPS tracking. Factors such as economic shifts, regulatory changes, and global events significantly influence the lay-up process, necessitating thorough planning to minimize vessel depreciation.
Ballasting, the process of adjusting ballast water to maintain stability, is a fundamental operational requirement for the maritime industry. Proper lay-up is vital for preserving a vessel's condition and ensuring its readiness for swift reactivation. By adopting comprehensive maintenance routines and timely reactivation strategies, shipowners can effectively minimize depreciation, reduce reactivation costs, and mitigate safety risks. Neglecting lay-up maintenance can lead to costly repairs and operational challenges.
Understanding Lay-Up Vessels
Lay-up vessels are ships temporarily taken out of service and moored for extended periods due to economic downturns, seasonal cargo shortages, or oversupply in the maritime industry. The primary benefit of lay-up is the reduction of operational expenses while preserving the vessel's overall value. However, managing the lay-up process—whether hot, warm, or cold—is complex due to the ship's size, intricacy, and exposure to harsh marine environments.
Effective lay-up management requires a comprehensive maintenance plan to prevent corrosion, fouling, and degradation of the vessel's infrastructure, machinery, and equipment. This includes regular preventive maintenance, system inspections, and tailored preservation strategies. The ultimate goal is to ensure the vessel can quickly return to operational status and meet class and statutory certification requirements at a reasonable cost when reactivated.
Location Selection
We are a class-certified lay-up service provider specializing in the professional management of all types of vessels, including offshore installations like oil rigs, drilling rigs, and survey vessels. Our commitment to excellence sets high standards in the industry, backed by a proven track record of managing over 200 vessels. We deliver cold lay-up solutions through highly trained professionals and established processes, and we are fully licensed by "The Director of Ports and Harbors; Sabah" for operations in Labuan, East Malaysia.
Choosing the right location for vessel lay-up is crucial, as it directly impacts the safety and preservation of the ships during their dormant period. The following criteria are essential in selecting a lay-up site that ensures the vessel's protection and readiness for swift reactivation:
- Security: The chosen site must be safe from pirates, politically stable, and have support from local security in case of emergencies to prevent unauthorized access, vandalism, or theft. A secure location deters potential risks and protects the vessel throughout the lay-up period.
- Anchoring Ground Quality: A ship's anchoring system relies heavily on the quality of the seabed. Optimal holding conditions, typically found at depths between 22 and 30 meters, are crucial for preventing the vessel from drifting or capsizing, thereby safeguarding both the ship and its anchoring equipment.
- Regulatory Adherence: Strict adherence to both local and international regulations is paramount for successful lay-up anchorage. All environmental, safety, and maritime protocols must be observed when establishing a site. Official gazetting and certification of the location as a lay-up anchorage are essential. By complying with these requirements, we mitigate legal risks, honour the ship’s flag state obligations, and prevent costly penalties.
- Environmental Conditions: A lay-up site in Brunei Bay offers several advantages, including its sheltered location outside the typhoon belt and gentle currents under 1 knot, which enhance vessel safety and reduce potential damage and wear and tear. Additionally, its strategic position provides potential logistical benefits.
- Accessibility: Labuan is an ideal location due to its proximity for efficient crew changes, supply replenishment, and swift emergency response. The island's international airport facilitates convenient access for vessel owners and representatives. Additionally, the availability of technical support for vessel maintenance and marine asset management is crucial.
Safe Practices and Procedures
Ensuring the safety of vessels during lay-up requires a comprehensive set of measures and protocols designed to protect the ship from potential hazards. The following are essential safety practices that should be implemented:
- Bilge and Fire Alarms: It's crucial to maintain bilge and fire alarm systems. These systems need to work properly to give early warnings in case of water entry or fire. Sensors placed in the aft and forward sections of the engine room and near the forecastle detect water ingress. If water levels rise, a bilge floater triggers an alarm in the watchmen's hut. Fire and smoke detectors are strategically located in the accommodation, engine room, and forward compartment to detect fire hazards. An efficient emergency response plan and a well-trained team are in place to respond promptly. Keeping these systems in optimal condition is important to ensure safety, as water ingress and fire are the most dangerous threats to an idle vessel.
- Security Patrols: It is essential to continuously monitor the lay-up vessel to prevent unauthorized access, theft, or safety hazards. Regular patrolling is crucial for identifying potential problems. On-board watchmen conduct rounds checks and report to the Base Radio Room. Data from these patrols is collected and logged for record keeping and used for reporting.
- Weather Monitoring: Monitoring weather patterns is essential for predicting adverse conditions and planning. A real-time weather monitoring system enables proactive measures by allowing for the implementation of preventive actions to minimize the impact of extreme weather.
- Security Seals: Weekly inspections of the seals are crucial to ensure all areas are well-maintained. Additionally, safety seals offer an extra layer of security by providing peace of mind that valuable and important items are securely stored in a sealed compartment of the owner's choice.
- Dehumidification: Utilizing correct and effective dehumidification techniques in the facility can prevent moisture-related failures and corrosion and maintain the vessel's condition during lay-up.
- Pest Control: Pest control is necessary to prevent infestation of key components like wiring and insulation..
- Vessel Movement: All vessels have GPS monitoring systems to ensure movement remains within safe margins. Any abnormal movement is reported immediately to the Base Radio Room and the emergency response team for further action.
- Wind Conditions: An anemometer monitors wind speed, and safety advisories are issued to watchmen and crew during strong wind forecasts. The Radio Room operator collects data from watchmen’s reports, updates the emergency response team on adverse weather, and shares this information with other vessels in the lay-up area for safety precautions.
Sealing and Humidity Control
Minimizing corrosion and equipment degradation during vessel lay-up requires the implementation of effective preservation methods. Essential strategies involve creating a controlled environment by sealing the vessel to reduce humidity and maintaining optimal moisture levels throughout its interior.
Compartmental Sealing for Dehumidification
Compartmental sealing involves establishing a controlled, dry-air environment within the vessel’s critical spaces, particularly those housing essential machinery and electronic equipment. This is accomplished by sealing all openings such as doors, hatches, and ventilation ducts using airtight gaskets or temporary cladding. Once the vessel is sealed, a dehumidification system is deployed to regulate the internal atmosphere. By circulating dry air and effectively removing moisture, the system maintains low relative humidity, significantly reducing the risk of corrosion and equipment degradation.
Humidity Level Maintenance
Maintaining optimal humidity levels is crucial for safeguarding metal surfaces, electrical circuits, and other sensitive components from moisture-related damage. Hygroscopic materials like silica gel can be placed within sealed compartments, such as electrical switchboards, to absorb excess moisture from the air. Regular monitoring with hygrometers or humidity sensors ensures that conditions remain within the desired range. Additionally, corrosion inhibitors, when applied in FO tanks or ballast tanks with the owner’s consent, offer an extra layer of protection by releasing chemicals that prevent corrosion on metal surfaces.
Maintenance Routine
Maintaining the integrity of a vessel during lay-up is essential to ensure its longevity and readiness for reactivation. Here are some strategies that focus on hull protection, equipment maintenance, and anchor chain management:
- Hull Protection
- Regular Inspections: Conduct periodic underwater inspections by divers to check for hull condition and integrity, including potential corrosion or biofouling, and ensure that sea overboard valves are functioning correctly and their openings are clear.
- Anodes: Install additional sacrificial anodes to protect the hull from electrolytic corrosion.
- Cleaning: Perform underwater hull cleaning before reactivation to remove marine growth, which can contribute to increased fuel consumption after reactivation.
- Equipment Maintenance
- Machinery Preservation: Rotate machinery periodically to prevent seizure and lubricate moving parts to protect against rust.
- Electrical Systems: Conduct insulation resistance tests on electrical equipment during lay-up to prevent the deterioration of electrical components.
- Critical Spares: Store critical spare parts in a controlled environment to prevent damage from humidity or temperature fluctuations.
- Anchor Chain Management
- Inspection: Inspect anchor chains for signs of wear and condition
- Maintenances: Heave up the anchor every 3 months to ensure the anchoring system is working properly and to prevent the anchor chain from being buried under the seabed, thereby avoiding localized wear and stress. The swivel installation on anchor chains can prevent kinking between the hawse pipe and waterline, minimizing anchor chain wear and tear.
- Monitoring: Monitor the tension and position of the anchor chain to ensure the vessel remains securely moored.
Reporting and Team Management
Effective reporting and team management are vital for maintaining a vessel during lay-up. These processes ensure meticulous monitoring of the vessel's condition and the efficient, safe execution of maintenance activities:
- Regular Reporting
- Condition Reports: Regular lay-up condition reports should document the vessel's systems and structure status. These reports provide a historical record and help identify trends or issues requiring attention.
- Maintenance Logs: Detailed maintenance logs are essential for tracking the work carried out on the vessel. They serve as a reference for future maintenance activities and verify compliance with regulatory requirements.
- Incident Reports: Prompt reporting is essential to document any incidents, detail the response, facilitate a review of procedures, and prevent future occurrences. Any incident reports will be sent to owners within 24 hours.
- Experienced Maintenance Teams
- Specialized Skills: Our team is led by an experienced maintenance engineer, maintaining a ratio of 1 maintenance engineer to 4 fully maintained vessels. Our maintenance teams consist of individuals with seagoing backgrounds and specialized skills relevant to the vessel's systems and equipment. Their expertise ensures that maintenance tasks are performed correctly and efficiently.
- Team Coordination: Effective coordination among team members is vital. Clear communication channels and defined roles help streamline maintenance activities and prevent overlaps or gaps in responsibilities.
- Continuous Training: Ongoing training for maintenance teams is important to keep their skills up to date, especially with the introduction of new technologies or changes in industry standards.
- Ongoing Safety Training
- Safety Protocols: Regular safety seminars with the latest safety protocols and required training are carried out for our onboard team members.
- Drills and Exercises: Conducting drills and exercises, simulates real-life scenarios, helping teams practice their response to emergencies and refine their skills.
- Safety Culture: Fostering a culture of safety within the team encourages proactive and thorough risk assessment and mitigation, leading to a safer working environment.
Managing lay-up vessels is a nuanced and critical aspect of maritime operations, particularly when economic or operational circumstances necessitate a temporary cessation of a vessel’s active duties. Adhering to best practices in lay-up vessel management is crucial. These practices ensure the preservation of the vessel’s structural integrity, the reliability of its machinery, and the safety of its systems.
Effective lay-up management is pivotal. It is a strategic approach that protects the vessel’s value and ensures that it remains a ready and capable asset within the fleet. As the maritime industry adapts to the ever-changing tides of global commerce, effective vessel lay-up management remains a testament to the foresight and resilience of those who maintain our vessels, even when they are not in active service. Contact us today to learn more about our expert lay-up management services.